弹条扣件具有扣压力大、弹性好且能够保证轨距等优点[1-2],在我国铁路上已广泛使用。Ⅲ型弹条扣件是e型扣件的一种,适用于标准轨距铁路直线或半径R≥350m的曲线上铺设60kg/m钢轨和Ⅲ型无挡肩混凝土轨枕的无缝线路。扣压力是弹条的重要性能指标。文献[3]分析了Ⅲ型弹条不同加载位移与扣压力的关系。文献[4]研究了Ⅲ型弹条经预压强化后的扣压力。文献[5]通过有限元模拟及非线性接触理论研究了Ⅲ型弹条的受力情况。文献[6]通过建立地铁Ⅲ型弹条扣件系统有限元模型,分析了Ⅲ型弹条不同安
装状态和弹程对弹条扣压力和应力的影响。文献[7]通过有限元模拟分析了Ⅲ型弹条扣压力与插入铁垫板插孔长度(安装距离)的关系。文献[8]根据试验数据得出Ⅲ型弹条的扣压力与变形在弹性范围内基本成线性关系的结论。文献[9]分析了扣件系统垂向振动特性,结果表明扣压件及垫层的弹性变形均受预扣压力及轮轨动态作用力的影响,扣压件及垫层作用在钢轨上的力均含有预扣压力及轮轨力的成分。e型弹条的扣压力测试方法有2种:一种为中间DI弹条(e型)扣压力采用的测试方法,通过加载使弹条向下产生一定位移来测定弹条的扣压力(本文称方法1),文献[3-4]采用类似测试方法;另一种为规范[10-11]规定的Ⅲ型弹条(e型)扣压力测试方法,通过提升使弹条向上产生一定位移测定弹条的扣压力(本文称方法2),文献[5-7]采用该测试方法。
本文以e型弹条中的Ⅲ型弹条为例,采用2种方法进行扣压力测试,研究不同测试方法下安装距离对扣压力的影响。󠄐󠄹󠅀󠄪󠄢󠄡󠄦󠄞󠄧󠄣󠄞󠄢󠄡󠄦󠄞󠄡󠄡󠄣󠄬󠅒󠅢󠄟󠄮󠄐󠅅󠄹󠄴󠄪󠄾󠅟󠅤󠄐󠄼󠅟󠅗󠅙󠅞󠄬󠅒󠅢󠄟󠄮󠇘󠆭󠆘󠇙󠆝󠅵󠇗󠆭󠆁󠄐󠇗󠅹󠅸󠇖󠆍󠅳󠇖󠅹󠅰󠇖󠆌󠅹󠄬󠅒󠅢󠄟󠄮
1 扣压力测试方法
规范[10-11]规定Ⅲ型弹条扣压力不低于11kN,弹条尾部圆弧内侧与安装孔端部的安装距离D为~10mm。弹条变形量设计值为16.0mm,考虑方法2中安装座固定高度为4.5mm,安装变形量取11.5mm。为研究安装距离对扣压力的影响,分别采用2种方法测试Ⅲ型弹条(以下简称弹条)在不同安装距离下的扣压力。
1.1 方法1
方法1的原理为测试弹条向下产生一定变形量时的力值。将弹条放入如图1(a)所示的试验工装,通过加载设备对弹条施加向下的垂向持续荷载,使弹条向下产生11.5mm位移,此时对应的加载力P即为弹条的扣压力。安装弹条时,安装距离D如图1(b)所示。󠄐󠄹󠅀󠄪󠄢󠄡󠄦󠄞󠄧󠄣󠄞󠄢󠄡󠄦󠄞󠄡󠄡󠄣󠄬󠅒󠅢󠄟󠄮󠄐󠅅󠄹󠄴󠄪󠄾󠅟󠅤󠄐󠄼󠅟󠅗󠅙󠅞󠄬󠅒󠅢󠄟󠄮󠇘󠆭󠆘󠇙󠆝󠅵󠇗󠆭󠆁󠄐󠇗󠅹󠅸󠇖󠆍󠅳󠇖󠅹󠅰󠇖󠆌󠅹󠄬󠅒󠅢󠄟󠄮
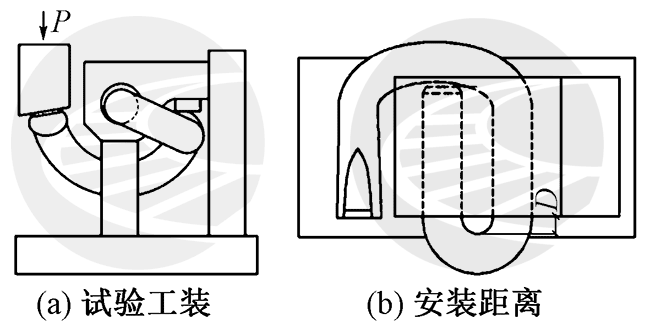
图1 方法1测试示意
方法1的测试设备为专用加载工装和专用加载设备,操作简单,可进行不同加载位移、不同加载力的加载试验,准确性高。
1.2 方法2
方法2的原理为测试弹条向上提升一定变形量时的力值。用专用工具将被测弹条按标准组装状态安装在安装座上(图2),弹条安装于安装座后变形量为11.5mm。安放夹持工装夹住弹条趾端,钩子外侧面距离弹条趾端端部约5mm。用加载设备对夹持工装施加垂直于安装座底板的荷载,夹持工装夹住弹条缓慢提升。当弹条趾端下表面与安装座之间刚好能插入0.1mm的塞尺时,此时的拉力F即为弹条扣压力。󠄐󠄹󠅀󠄪󠄢󠄡󠄦󠄞󠄧󠄣󠄞󠄢󠄡󠄦󠄞󠄡󠄡󠄣󠄬󠅒󠅢󠄟󠄮󠄐󠅅󠄹󠄴󠄪󠄾󠅟󠅤󠄐󠄼󠅟󠅗󠅙󠅞󠄬󠅒󠅢󠄟󠄮󠇘󠆭󠆘󠇙󠆝󠅵󠇗󠆭󠆁󠄐󠇗󠅹󠅸󠇖󠆍󠅳󠇖󠅹󠅰󠇖󠆌󠅹󠄬󠅒󠅢󠄟󠄮
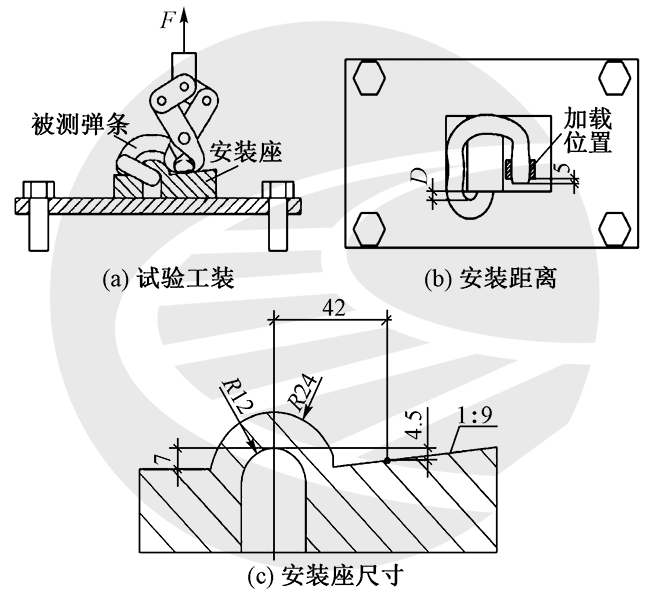
图2 方法2测试示意
方法2的测试设备为专用加载工装和专用加载设备,操作简单,加载方式单一,准确性高。
2 测试结果与分析
采用2种方法,分别测试D为8,10,20mm时的扣压力。每个安装距离下测试5件弹条的扣压力,取其平均值作为该安装距离下的扣压力测试值。󠄐󠄹󠅀󠄪󠄢󠄡󠄦󠄞󠄧󠄣󠄞󠄢󠄡󠄦󠄞󠄡󠄡󠄣󠄬󠅒󠅢󠄟󠄮󠄐󠅅󠄹󠄴󠄪󠄾󠅟󠅤󠄐󠄼󠅟󠅗󠅙󠅞󠄬󠅒󠅢󠄟󠄮󠇘󠆭󠆘󠇙󠆝󠅵󠇗󠆭󠆁󠄐󠇗󠅹󠅸󠇖󠆍󠅳󠇖󠅹󠅰󠇖󠆌󠅹󠄬󠅒󠅢󠄟󠄮
2.1方法1结果与分析
采用方法1测试时,每件弹条仅进行某一安装距离下的扣压力测量。测得D为8,10,20mm时扣压力分别为11.6,11.8,12.1kN。安装距离与扣压力关系曲线见图3。可知:采用方法1进行测试,各安装距离下的扣压力均大于11kN,满足标准要求;弹条的扣压力随安装距离的增大而增大。󠄐󠄹󠅀󠄪󠄢󠄡󠄦󠄞󠄧󠄣󠄞󠄢󠄡󠄦󠄞󠄡󠄡󠄣󠄬󠅒󠅢󠄟󠄮󠄐󠅅󠄹󠄴󠄪󠄾󠅟󠅤󠄐󠄼󠅟󠅗󠅙󠅞󠄬󠅒󠅢󠄟󠄮󠇘󠆭󠆘󠇙󠆝󠅵󠇗󠆭󠆁󠄐󠇗󠅹󠅸󠇖󠆍󠅳󠇖󠅹󠅰󠇖󠆌󠅹󠄬󠅒󠅢󠄟󠄮
.png)
图3 安装距离与扣压力关系曲线(方法1)
采用方法1测试时,随着安装距离的增加,弹条与工装的接触区域由小变大(图4),接触面积的增大意味着产生同样塑性变形量(位移)所需的力增大,即扣压力增大
.png)
图4 不同安装距离下的接触区域(方法1)
2.2方法2结果与分析
采用方法2测试时,每件弹条分别在D为8,10,20mm时进行扣压力测量。测得D为8,10,20mm时扣压力分别为12.9,12.3,9.9kN。安装距离与扣压力关系曲线见图5。󠄐󠄹󠅀󠄪󠄢󠄡󠄦󠄞󠄧󠄣󠄞󠄢󠄡󠄦󠄞󠄡󠄡󠄣󠄬󠅒󠅢󠄟󠄮󠄐󠅅󠄹󠄴󠄪󠄾󠅟󠅤󠄐󠄼󠅟󠅗󠅙󠅞󠄬󠅒󠅢󠄟󠄮󠇘󠆭󠆘󠇙󠆝󠅵󠇗󠆭󠆁󠄐󠇗󠅹󠅸󠇖󠆍󠅳󠇖󠅹󠅰󠇖󠆌󠅹󠄬󠅒󠅢󠄟󠄮
.png)
图5 安装距离与扣压力关系曲线(方法2)
由图5可知:采用方法2进行测试,D为8,10mm时扣压力满足标准要求,D为20mm时扣压力小于11kN,不满足要求;弹条的扣压力随安装距离的增大而减小。这是因为弹条的安装变形使不同距离下弹条与工装的接触位置不同,如图6所示。进行扣压力测试时,D为8,10mm时接触位置为过渡圆弧处(A区域),D为20mm时接触位置为中肢上表面(B区域)。加载前,将扣压面抬高至规定高度过程中要克服扣压面与工装台面的作用力,即预紧力。预紧力越小,需要的最终外力(扣压力)也越小。从图6可以看出,随着安装距离的增加,弹条与工装接触位置高度由h降为h1,造成预紧力下降。因此,随着安装距离的增大,弹条的扣压力有所减小。
.png)
图6 安装变形示意(方法2)
采用方法2测试时,随着安装距离的增大,接触位置由A区域变成B区域,弹条与工装的接触面积增大,即扣压力随接触面积增大而减小。这与方法1得出的接触面积增大造成扣压力增大的结论相悖。对比2种方法试验数据可知,采用方法1测试时安装距离从8mm到10mm、从10mm到20mm扣压力分别增加了0.2,0.3kN;采用方法2测试时安装距离从8mm到10mm、从10mm到20mm扣压力分别减小了0.6,2.4kN。显然,方法1中弹条因接触区域增大对扣压力的影响远小于方法2中安装变形对扣压力的影响。
2.3 2种方法的扣压力试验结果对比对比
2种方法测得的扣压力发现,D为8,10mm时,方法1的扣压力小于方法2;D为20mm时,方法1的扣压力大于方法2。这是因为用方法1测试时弹条在3种安装距离下的加载位移始终为11.5mm,而采用方法2时由于安装座的尺寸、形状及弹条过渡圆弧的原因,使弹条在D为20mm时实际安装变形量低于11.5mm,D为8,10mm时实际安装变形量大于11.5mm。󠄐󠄹󠅀󠄪󠄢󠄡󠄦󠄞󠄧󠄣󠄞󠄢󠄡󠄦󠄞󠄡󠄡󠄣󠄬󠅒󠅢󠄟󠄮󠄐󠅅󠄹󠄴󠄪󠄾󠅟󠅤󠄐󠄼󠅟󠅗󠅙󠅞󠄬󠅒󠅢󠄟󠄮󠇘󠆭󠆘󠇙󠆝󠅵󠇗󠆭󠆁󠄐󠇗󠅹󠅸󠇖󠆍󠅳󠇖󠅹󠅰󠇖󠆌󠅹󠄬󠅒󠅢󠄟󠄮
3结论
根据采用2种测试方法获得的Ⅲ型弹条扣压力结果及安装距离与扣压力关系曲线,得出结论如下:󠄐󠄹󠅀󠄪󠄢󠄡󠄦󠄞󠄧󠄣󠄞󠄢󠄡󠄦󠄞󠄡󠄡󠄣󠄬󠅒󠅢󠄟󠄮󠄐󠅅󠄹󠄴󠄪󠄾󠅟󠅤󠄐󠄼󠅟󠅗󠅙󠅞󠄬󠅒󠅢󠄟󠄮󠇘󠆭󠆘󠇙󠆝󠅵󠇗󠆭󠆁󠄐󠇗󠅹󠅸󠇖󠆍󠅳󠇖󠅹󠅰󠇖󠆌󠅹󠄬󠅒󠅢󠄟󠄮
1)采用方法1测试时弹条扣压力随安装距离的增大而增大;采用方法2测试时弹条扣压力随安装距离的增大而减小。󠄐󠄹󠅀󠄪󠄢󠄡󠄦󠄞󠄧󠄣󠄞󠄢󠄡󠄦󠄞󠄡󠄡󠄣󠄬󠅒󠅢󠄟󠄮󠄐󠅅󠄹󠄴󠄪󠄾󠅟󠅤󠄐󠄼󠅟󠅗󠅙󠅞󠄬󠅒󠅢󠄟󠄮󠇘󠆭󠆘󠇙󠆝󠅵󠇗󠆭󠆁󠄐󠇗󠅹󠅸󠇖󠆍󠅳󠇖󠅹󠅰󠇖󠆌󠅹󠄬󠅒󠅢󠄟󠄮
2)采用方法1时,不同安装距离(8,10,20mm)的扣压力均满足标准要求;采用方法2时,安装距离为8,10mm时扣压力满足标准要求,安装距离为20mm时不满足要求。因此,采用方法2进行扣压力测试时须严格保证弹条与安装座距离处于8~10mm。󠄐󠄹󠅀󠄪󠄢󠄡󠄦󠄞󠄧󠄣󠄞󠄢󠄡󠄦󠄞󠄡󠄡󠄣󠄬󠅒󠅢󠄟󠄮󠄐󠅅󠄹󠄴󠄪󠄾󠅟󠅤󠄐󠄼󠅟󠅗󠅙󠅞󠄬󠅒󠅢󠄟󠄮󠇘󠆭󠆘󠇙󠆝󠅵󠇗󠆭󠆁󠄐󠇗󠅹󠅸󠇖󠆍󠅳󠇖󠅹󠅰󠇖󠆌󠅹󠄬󠅒󠅢󠄟󠄮
文章来源:
原文名称:Ⅲ型弹条扣压力测试方法󠄐󠄹󠅀󠄪󠄢󠄡󠄦󠄞󠄧󠄣󠄞󠄢󠄡󠄦󠄞󠄡󠄡󠄣󠄬󠅒󠅢󠄟󠄮󠄐󠅅󠄹󠄴󠄪󠄾󠅟󠅤󠄐󠄼󠅟󠅗󠅙󠅞󠄬󠅒󠅢󠄟󠄮󠇘󠆭󠆘󠇙󠆝󠅵󠇗󠆭󠆁󠄐󠇗󠅹󠅸󠇖󠆍󠅳󠇖󠅹󠅰󠇖󠆌󠅹󠄬󠅒󠅢󠄟󠄮
作者信息:张松琦1 张远庆1 汝继来1 吕明奎2 朱继光2
作者单位:1.中国铁道科学研究院集团有限公司铁道建筑研究所,北京100081;2.北京铁科首钢轨道技术股份有限公司北京102206󠄐󠄹󠅀󠄪󠄢󠄡󠄦󠄞󠄧󠄣󠄞󠄢󠄡󠄦󠄞󠄡󠄡󠄣󠄬󠅒󠅢󠄟󠄮󠄐󠅅󠄹󠄴󠄪󠄾󠅟󠅤󠄐󠄼󠅟󠅗󠅙󠅞󠄬󠅒󠅢󠄟󠄮󠇘󠆭󠆘󠇙󠆝󠅵󠇗󠆭󠆁󠄐󠇗󠅹󠅸󠇖󠆍󠅳󠇖󠅹󠅰󠇖󠆌󠅹󠄬󠅒󠅢󠄟󠄮
期刊信息: 铁道建筑 2020, 60(4)󠄐󠄹󠅀󠄪󠄢󠄡󠄦󠄞󠄧󠄣󠄞󠄢󠄡󠄦󠄞󠄡󠄡󠄣󠄬󠅒󠅢󠄟󠄮󠄐󠅅󠄹󠄴󠄪󠄾󠅟󠅤󠄐󠄼󠅟󠅗󠅙󠅞󠄬󠅒󠅢󠄟󠄮󠇘󠆭󠆘󠇙󠆝󠅵󠇗󠆭󠆁󠄐󠇗󠅹󠅸󠇖󠆍󠅳󠇖󠅹󠅰󠇖󠆌󠅹󠄬󠅒󠅢󠄟󠄮
参考文献[s][p]
- [1]王其昌.无砟轨道钢轨扣件[M].成都:西南交通大学出版社,2006.[2]赵国堂.高速铁路无砟轨道结构[M].北京:中国铁道出版社,2006.
- [3]杨程亮.DT-Ⅲ型扣件弹条断裂原因分析[D].北京:中国铁道科学研究院,2019.
- [4]曾召林.Ⅲ型弹条变形强化的研究及实践[J].铁道工程学报,2001,18(3):132-134.
- [5]武青海,陈厚嫦,周虹伟,等.应用非线性接触理论分析弹条Ⅲ型扣件中弹条的应力和变形[J]. 中国铁道科学,2003,24(1):69-73.
- [6]尚红霞,温泽峰,吴磊,等.地铁扣件Ⅲ型弹条失效有限元分析[J].工程力学,2015,32(9):210-215.
- [7]张树峰,温泽峰,尚红霞,等.地铁扣件Ⅲ型弹条扣件铁垫板端部圆角优化分析[J]. 机械强度,2016,38(6):1335-1340.
- [8]丁娟娟,王孝羽,王倩云.DT-Ⅲ型扣件扣压力特性及动力特性试验研究[J].工程与建设,2019,33(2):230-233.
- [9]王开云,蔡成标,朱胜阳.铁路钢轨扣件系统垂向动力模型及振动特性[J].工程力学,2013,30(4):146-149,168
- [10]中国铁路总公司.弹条Ⅲ型扣件:Q/CR 565—2017[S].北京:中国铁道出版社,2017.
- [11]国家铁路局.高速铁路扣件第2部分:弹条Ⅳ型扣件:TB/T3395.2—2015[S].北京:中国铁道出版社,2016.
[/p]