0 前言
闪光焊是无缝钢轨生产及铺设的重要方法,它具有焊接效率高、焊接质量高的特点,其应用愈来愈广泛。闪光焊主要过程为闪平、预热、烧化、带电顶锻、无电顶锻、保压及推瘤,通过精确的程序控制、加压系统、加电系统等执行,整个过程在几分钟内完成。在钢轨焊接性能较好,各焊接参数较为匹配的情况下,焊接接头都能顺利通过超声波探伤等检验。然而在生产实际中常会出现焊接参数设置不合理、设备状态波动,导致焊接接头产生未熔合、夹渣、冷焊、过热、过烧、裂纹等缺陷[1-2]。准确识别这些缺陷才能制定正确的解决方案,这需要结合焊接工艺条件和显微分析来进行研究。在此结合U71Mn钢轨在某焊轨基地闪光焊探伤出现超使用标准的现象进行试验研究,通过分析接头显微形貌及焊接参数,判断缺陷产生的原因为过烧,通过调节焊接参数,消除了过烧现象。该试验结果用于指导钢轨焊接生产,保证了接头超声波探伤合格。
1 焊接条件
在某焊轨基地进行百米U71Mn 钢轨闪光焊对接焊,钢的主要化学成分如表1所示,其他有害残余元素控制较好。
表1 钢轨化学成分 (%)󠄐󠄹󠅀󠄪󠄢󠄡󠄦󠄞󠄧󠄣󠄞󠄢󠄡󠄦󠄞󠄡󠄡󠄠󠄬󠅒󠅢󠄟󠄮󠄐󠅅󠄹󠄴󠄪󠄾󠅟󠅤󠄐󠄼󠅟󠅗󠅙󠅞󠄬󠅒󠅢󠄟󠄮󠇘󠆭󠆘󠇙󠆝󠅵󠇗󠆭󠆁󠄐󠇗󠅹󠅸󠇖󠆍󠅳󠇖󠅹󠅰󠇖󠆌󠅹󠄬󠅒󠅢󠄟󠄮
w(C) | w(Si) | w(Mn) | w(P) | w(S) |
0.72 | 0.34 | 0.99 | 0.015 | 0.004 |
焊机为瑞士Schlatter GAAS80预热闪光焊接系统,功能先进。焊接流程为打磨→配轨→焊接→推瘤,焊接完毕后,检测焊头外形尺寸、粗磨及精磨、正火、超声波探伤。闪光焊试验主要参数如表2所示。第1组参数与生产所用相同,第2 组参数为改进后参数。
表2 闪光焊主要参数󠄐󠄹󠅀󠄪󠄢󠄡󠄦󠄞󠄧󠄣󠄞󠄢󠄡󠄦󠄞󠄡󠄡󠄠󠄬󠅒󠅢󠄟󠄮󠄐󠅅󠄹󠄴󠄪󠄾󠅟󠅤󠄐󠄼󠅟󠅗󠅙󠅞󠄬󠅒󠅢󠄟󠄮󠇘󠆭󠆘󠇙󠆝󠅵󠇗󠆭󠆁󠄐󠇗󠅹󠅸󠇖󠆍󠅳󠇖󠅹󠅰󠇖󠆌󠅹󠄬󠅒󠅢󠄟󠄮
参数序号 | 闪平时间 | 预热 | 烧化时间 | 末期烧化速度 | 顶锻时间 | 顶锻量 | 试样数 |
t/s | t/s | v/mm·s-1 | t/s | /mm | |||
1 | 20 | ① | 45 | 0.25 | 5 | 14 | |
2 | 20 | ② | 30 | 2.4 | 5 | 11 |
2 焊接接头缺陷
采用表2 所示的第1组参数进行焊接试验。总体上讲,焊接装配较好,实时焊接参数曲线稳定,接头推瘤时处于亮红状态,温度较均匀。
打磨焊头,冷却至40 益以下后进行超声波探伤。为了节约时间,部分焊头在焊态下探伤。探伤仪为CTS-1003 便携式超声波探伤仪,探伤时要注意辩识焊筋波及纯表面波。󠄐󠄹󠅀󠄪󠄢󠄡󠄦󠄞󠄧󠄣󠄞󠄢󠄡󠄦󠄞󠄡󠄡󠄠󠄬󠅒󠅢󠄟󠄮󠄐󠅅󠄹󠄴󠄪󠄾󠅟󠅤󠄐󠄼󠅟󠅗󠅙󠅞󠄬󠅒󠅢󠄟󠄮󠇘󠆭󠆘󠇙󠆝󠅵󠇗󠆭󠆁󠄐󠇗󠅹󠅸󠇖󠆍󠅳󠇖󠅹󠅰󠇖󠆌󠅹󠄬󠅒󠅢󠄟󠄮
第1组参数焊接接头探伤结果如表3 所示。󠄐󠄹󠅀󠄪󠄢󠄡󠄦󠄞󠄧󠄣󠄞󠄢󠄡󠄦󠄞󠄡󠄡󠄠󠄬󠅒󠅢󠄟󠄮󠄐󠅅󠄹󠄴󠄪󠄾󠅟󠅤󠄐󠄼󠅟󠅗󠅙󠅞󠄬󠅒󠅢󠄟󠄮󠇘󠆭󠆘󠇙󠆝󠅵󠇗󠆭󠆁󠄐󠇗󠅹󠅸󠇖󠆍󠅳󠇖󠅹󠅰󠇖󠆌󠅹󠄬󠅒󠅢󠄟󠄮
表3 焊接接头探伤结果(第1组参数)󠄐󠄹󠅀󠄪󠄢󠄡󠄦󠄞󠄧󠄣󠄞󠄢󠄡󠄦󠄞󠄡󠄡󠄠󠄬󠅒󠅢󠄟󠄮󠄐󠅅󠄹󠄴󠄪󠄾󠅟󠅤󠄐󠄼󠅟󠅗󠅙󠅞󠄬󠅒󠅢󠄟󠄮󠇘󠆭󠆘󠇙󠆝󠅵󠇗󠆭󠆁󠄐󠇗󠅹󠅸󠇖󠆍󠅳󠇖󠅹󠅰󠇖󠆌󠅹󠄬󠅒󠅢󠄟󠄮
状态 | 增益/dB | 位置/mm | 波峰幅度/% |
正火 | 75 | 水平30,水平37,水平43 | 14,18,10 |
焊态 | 75 | 水平35,水平41,水平45 | 10,18,18 |
正火 | 84 | 水平47,水平39,水平33 | 13,33,22 |
焊头探伤波峰10%~33%,以10%~18%居多,正火态探伤结果略好于焊态。缺陷主要集中在轨底离钢轨中心约40 mm范围内的近表面。
钢轨闪光焊常见缺陷如下:
(1)灰斑
存在于闪光焊焊缝断口中的局部光滑区域,与周边金属有明显界限。钢轨焊接灰斑可分为亮灰斑和暗灰斑。通常认为,灰斑产生的原因是钢轨焊接时Si、Mn、Al 等合金元素形成氧化物。在顶锻时,熔化的金属与这些夹杂物一起被挤压,沿工件径向流动排溢,未被排挤干净而残留在焊缝中的氧化物形成了断口上的灰斑。暗灰斑主要是由于闪光焊接时供给热量不足所致,增加热量供给后,暗灰斑就转化成亮灰斑或者基本消除[3]。不过灰斑难以用超声波探出。
(2)未熔合
焊头上母材与母材之间未能完全结合的部分一般出现在焊缝上。产生的原因主要有:a.轨端除锈不彻底,有污物;b. 两个接头端面间隙过大,顶锻量过小或过早,加热时间短,焊接温度达不到要求,闪光不稳定。未熔合可以通过超声波探出。󠄐󠄹󠅀󠄪󠄢󠄡󠄦󠄞󠄧󠄣󠄞󠄢󠄡󠄦󠄞󠄡󠄡󠄠󠄬󠅒󠅢󠄟󠄮󠄐󠅅󠄹󠄴󠄪󠄾󠅟󠅤󠄐󠄼󠅟󠅗󠅙󠅞󠄬󠅒󠅢󠄟󠄮󠇘󠆭󠆘󠇙󠆝󠅵󠇗󠆭󠆁󠄐󠇗󠅹󠅸󠇖󠆍󠅳󠇖󠅹󠅰󠇖󠆌󠅹󠄬󠅒󠅢󠄟󠄮
(3)裂纹
一般产生于轨脚端部,是在焊缝轨脚两端出现开裂的现象。这种缺陷对焊接接头整体力学性能影响很大。轨脚端部裂纹多数与焊接工艺有关,例如,焊接顶锻量不足,使轨脚部位的挤压面积小于钢轨端面,推凸和保压的时间过短,造成塑性变形量不足;焊接加热的时间不够长,造成加热范围过窄等。裂纹可以通过超声波探出。󠄐󠄹󠅀󠄪󠄢󠄡󠄦󠄞󠄧󠄣󠄞󠄢󠄡󠄦󠄞󠄡󠄡󠄠󠄬󠅒󠅢󠄟󠄮󠄐󠅅󠄹󠄴󠄪󠄾󠅟󠅤󠄐󠄼󠅟󠅗󠅙󠅞󠄬󠅒󠅢󠄟󠄮󠇘󠆭󠆘󠇙󠆝󠅵󠇗󠆭󠆁󠄐󠇗󠅹󠅸󠇖󠆍󠅳󠇖󠅹󠅰󠇖󠆌󠅹󠄬󠅒󠅢󠄟󠄮
(4)过烧
焊接时加热温度过高,局部金属熔化或接近熔化状态而造成的晶界偏析和烧熔,在外力作用下甚至会出现孔洞或裂缝。过烧是焊接接头最危险的缺陷之一,常出现在轨底两侧的轨脚位置。󠄐󠄹󠅀󠄪󠄢󠄡󠄦󠄞󠄧󠄣󠄞󠄢󠄡󠄦󠄞󠄡󠄡󠄠󠄬󠅒󠅢󠄟󠄮󠄐󠅅󠄹󠄴󠄪󠄾󠅟󠅤󠄐󠄼󠅟󠅗󠅙󠅞󠄬󠅒󠅢󠄟󠄮󠇘󠆭󠆘󠇙󠆝󠅵󠇗󠆭󠆁󠄐󠇗󠅹󠅸󠇖󠆍󠅳󠇖󠅹󠅰󠇖󠆌󠅹󠄬󠅒󠅢󠄟󠄮
轻度过烧时出现细小炭黑斑点,严重过烧时出现黑色蜂窝状组织[4]。产生过烧的原因有:a. 燃烧时间过长;b. 顶锻时间设置过短;c. 烧化末期速度过慢。在超探时,过烧会显示出缺陷波。󠄐󠄹󠅀󠄪󠄢󠄡󠄦󠄞󠄧󠄣󠄞󠄢󠄡󠄦󠄞󠄡󠄡󠄠󠄬󠅒󠅢󠄟󠄮󠄐󠅅󠄹󠄴󠄪󠄾󠅟󠅤󠄐󠄼󠅟󠅗󠅙󠅞󠄬󠅒󠅢󠄟󠄮󠇘󠆭󠆘󠇙󠆝󠅵󠇗󠆭󠆁󠄐󠇗󠅹󠅸󠇖󠆍󠅳󠇖󠅹󠅰󠇖󠆌󠅹󠄬󠅒󠅢󠄟󠄮
(5)焊缝夹杂物
焊缝夹杂物是指分布在熔化焊缝中的非金属氧化物颗粒。若将焊缝打断后,在宏观下观察时颜色较深。闪光焊氧化物夹杂产生的原因较多,并且难以掌握规律,一般认为是钢轨在焊接过程中,焊缝处有时形成硅酸盐类的非金属物质,少量聚集在闪光弧坑的底部,当最终的顶锻完成后,没有将非金属物质挤出,使其滞留在焊缝中,这样就形成了焊缝夹杂物。焊缝夹杂物可以通过超声波探出。󠄐󠄹󠅀󠄪󠄢󠄡󠄦󠄞󠄧󠄣󠄞󠄢󠄡󠄦󠄞󠄡󠄡󠄠󠄬󠅒󠅢󠄟󠄮󠄐󠅅󠄹󠄴󠄪󠄾󠅟󠅤󠄐󠄼󠅟󠅗󠅙󠅞󠄬󠅒󠅢󠄟󠄮󠇘󠆭󠆘󠇙󠆝󠅵󠇗󠆭󠆁󠄐󠇗󠅹󠅸󠇖󠆍󠅳󠇖󠅹󠅰󠇖󠆌󠅹󠄬󠅒󠅢󠄟󠄮
(6)粗晶组织
采用超声波探伤检查钢轨焊接接头,有时轨头焊缝处会出现“缺陷波”,若对锯切钢轨接头焊缝进行解剖分析,难见到其存在缺陷。金相分析表明,“缺陷波”来自钢轨接头心部因热处理工艺不当产生的粗晶组织。󠄐󠄹󠅀󠄪󠄢󠄡󠄦󠄞󠄧󠄣󠄞󠄢󠄡󠄦󠄞󠄡󠄡󠄠󠄬󠅒󠅢󠄟󠄮󠄐󠅅󠄹󠄴󠄪󠄾󠅟󠅤󠄐󠄼󠅟󠅗󠅙󠅞󠄬󠅒󠅢󠄟󠄮󠇘󠆭󠆘󠇙󠆝󠅵󠇗󠆭󠆁󠄐󠇗󠅹󠅸󠇖󠆍󠅳󠇖󠅹󠅰󠇖󠆌󠅹󠄬󠅒󠅢󠄟󠄮
钢轨闪光焊接头实物、横截面如图1所示,钢轨由轨头、轨腰及轨底组成。沿焊头纵向从中心切开取样,如图1b 所示。磨光截面,腐蚀后观察到的宏观形貌如图1c 所示,焊接亮线略宽,流线无明显异常。可以看出,由于钢轨形状呈I字形,较为复杂,所取截面上焊接流线在轨头及轨底有明显转向,而在轨腰部位则看不到转向。实际上,轨腰部位的焊接流线也有转向,但因为取样截面与轨腰表面平行,从该方向显示不出。󠄐󠄹󠅀󠄪󠄢󠄡󠄦󠄞󠄧󠄣󠄞󠄢󠄡󠄦󠄞󠄡󠄡󠄠󠄬󠅒󠅢󠄟󠄮󠄐󠅅󠄹󠄴󠄪󠄾󠅟󠅤󠄐󠄼󠅟󠅗󠅙󠅞󠄬󠅒󠅢󠄟󠄮󠇘󠆭󠆘󠇙󠆝󠅵󠇗󠆭󠆁󠄐󠇗󠅹󠅸󠇖󠆍󠅳󠇖󠅹󠅰󠇖󠆌󠅹󠄬󠅒󠅢󠄟󠄮
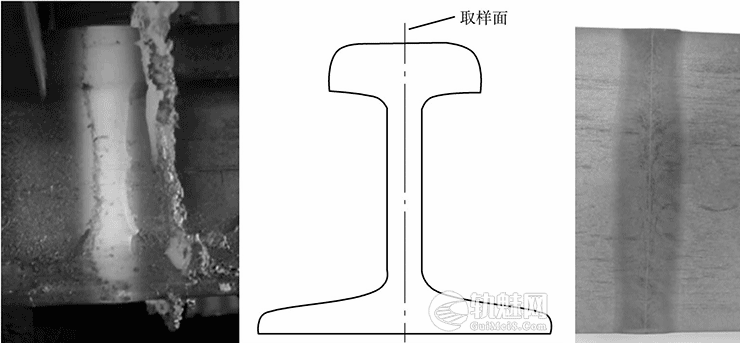
a 实际焊头 b 焊轨横截面及取样方向 c 接头宏观形貌渊焊态冤
图1焊头形状及接头宏观形貌
对焊头的焊接缺陷进行显微分析,焊头的主要缺陷位于轨底焊缝亮线附近的近表面区,如图2 所示。其中多数缺陷如图2a、2b所示,距离熔合线(亮线)0.2~0.9 mm;也有很少量缺陷位于亮线上,如图2c所示。
初看图2a 的缺陷,与文献[6]介绍的推凸裂纹非常相近。推凸裂纹产生的原因是焊接末期顶锻完成后要进行推瘤,推瘤刀从焊接区一侧向另一侧移动(见图1a),另一侧带状组织受垂向力产生较最大弯曲,因偏析、非金属杂夹、推瘤温度低塑性差而产生裂纹。不过试验用钢轨钢质较纯,含S 量低;焊接实验时,推瘤时温度较高,基本上可以排除推瘤缺陷。

a 推瘤处亮线及其附近缺陷 b 亮线附近缺陷 c 亮线上缺陷
图2 焊接缺陷
探伤缺陷区域组织为细片状珠光体+粗片状珠光体,焊接熔合线组织为网状铁素体+珠光体。对缺陷进行进一步分析,大部分缺陷是孔洞,用扫描电镜观看,不到明显夹渣。只有少量缺陷的裂缝尖端及局部裂缝壁上有硫化锰夹杂物,如图3 所示。微观分析显示,硫化物等夹杂及其他夹渣并非形成缺陷的主要原因。
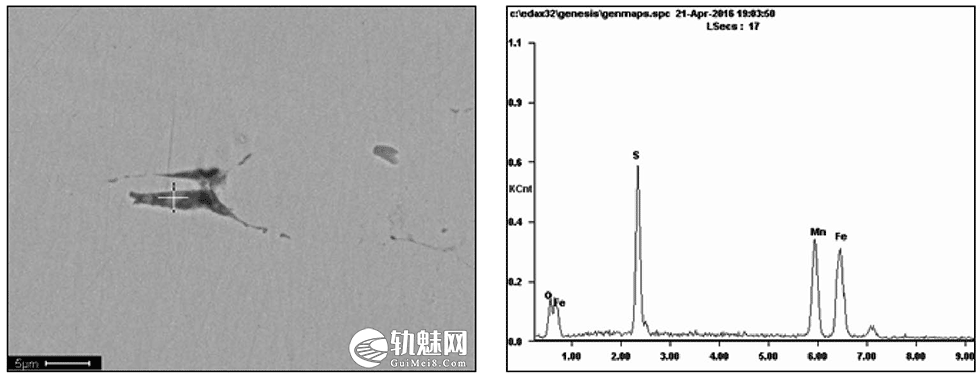
图3 少数缺陷上硫化物
对焊头进行落锤试验,在不开口情况下4~5 次落锤打不断,说明即使焊头中存在这种过烧缺陷,其仍具有较强的抗落锤打击能力。开口后打断,观看断口发现,断口灰斑很少,落锤性能较好。但断口显示出过热特征,加热与挤压不匹配导致出现近缝近表面缺陷。
这类缺陷为过烧的可能性很大。过烧时,加热温度梯度过小、热影响区过宽。过烧会导致晶粒边界熔化,产生体积型缺陷,存在于焊缝或热影响区。󠄐󠄹󠅀󠄪󠄢󠄡󠄦󠄞󠄧󠄣󠄞󠄢󠄡󠄦󠄞󠄡󠄡󠄠󠄬󠅒󠅢󠄟󠄮󠄐󠅅󠄹󠄴󠄪󠄾󠅟󠅤󠄐󠄼󠅟󠅗󠅙󠅞󠄬󠅒󠅢󠄟󠄮󠇘󠆭󠆘󠇙󠆝󠅵󠇗󠆭󠆁󠄐󠇗󠅹󠅸󠇖󠆍󠅳󠇖󠅹󠅰󠇖󠆌󠅹󠄬󠅒󠅢󠄟󠄮
图2的焊接缺陷形态具有过烧特征。󠄐󠄹󠅀󠄪󠄢󠄡󠄦󠄞󠄧󠄣󠄞󠄢󠄡󠄦󠄞󠄡󠄡󠄠󠄬󠅒󠅢󠄟󠄮󠄐󠅅󠄹󠄴󠄪󠄾󠅟󠅤󠄐󠄼󠅟󠅗󠅙󠅞󠄬󠅒󠅢󠄟󠄮󠇘󠆭󠆘󠇙󠆝󠅵󠇗󠆭󠆁󠄐󠇗󠅹󠅸󠇖󠆍󠅳󠇖󠅹󠅰󠇖󠆌󠅹󠄬󠅒󠅢󠄟󠄮
3 过烧缺陷的消除
焊接参数调节及试验结果为表2 中的第2 组参数。与第1组参数相比,烧化时间由45s减至30s,末期烧化速度由0.25 mm/s 增至2.40 mm/s,顶锻量由14 mm 减至11 mm,焊接5 个接头,焊后正火处理后再进行超声波探伤,5个焊头反射波均很小。进行落锤试验时,两锤打击后均未断裂。
本研究试验钢含S 量低,炼钢时有害微量元素控制较好,因此,在正常焊接参数条件下,热影响区不会产生明显的晶界熔化,形成类似过烧的缺陷。但在焊接参数匹配不当的情况下,低熔点偏析晶界熔化较多,还会进一步加剧低熔点物质的偏析和聚焦,扩大熔化区的范围,在冷却过程中及力的作用下形成孔洞及裂纹,导致探伤不合格。另外,由于这种过烧缺陷出现于熔合线附近的母材上,使人很容易错误地将其产生原因归咎于母材不纯,给问题的解决带来很大麻烦,甚至造成不必要的严重损失。󠄐󠄹󠅀󠄪󠄢󠄡󠄦󠄞󠄧󠄣󠄞󠄢󠄡󠄦󠄞󠄡󠄡󠄠󠄬󠅒󠅢󠄟󠄮󠄐󠅅󠄹󠄴󠄪󠄾󠅟󠅤󠄐󠄼󠅟󠅗󠅙󠅞󠄬󠅒󠅢󠄟󠄮󠇘󠆭󠆘󠇙󠆝󠅵󠇗󠆭󠆁󠄐󠇗󠅹󠅸󠇖󠆍󠅳󠇖󠅹󠅰󠇖󠆌󠅹󠄬󠅒󠅢󠄟󠄮
4 结论
(1)钢轨闪光焊探伤不合格,其缺陷主要为焊缝附近存在孔洞及裂纹,且孔洞及裂纹上鲜有夹杂物,这是焊接参数不合适过烧造成的。
(2)通过调节末期烧化速度及顶锻时间,合理匹配焊接热输入及烧化、顶锻等参数。适当增加加热温度梯度,减少焊接热影响区过热区宽度,焊头探伤情况明显改善且合格。󠄐󠄹󠅀󠄪󠄢󠄡󠄦󠄞󠄧󠄣󠄞󠄢󠄡󠄦󠄞󠄡󠄡󠄠󠄬󠅒󠅢󠄟󠄮󠄐󠅅󠄹󠄴󠄪󠄾󠅟󠅤󠄐󠄼󠅟󠅗󠅙󠅞󠄬󠅒󠅢󠄟󠄮󠇘󠆭󠆘󠇙󠆝󠅵󠇗󠆭󠆁󠄐󠇗󠅹󠅸󠇖󠆍󠅳󠇖󠅹󠅰󠇖󠆌󠅹󠄬󠅒󠅢󠄟󠄮
文章来源:
原文名称 :钢轨闪光焊过烧缺陷识别与消除󠄐󠄹󠅀󠄪󠄢󠄡󠄦󠄞󠄧󠄣󠄞󠄢󠄡󠄦󠄞󠄡󠄡󠄠󠄬󠅒󠅢󠄟󠄮󠄐󠅅󠄹󠄴󠄪󠄾󠅟󠅤󠄐󠄼󠅟󠅗󠅙󠅞󠄬󠅒󠅢󠄟󠄮󠇘󠆭󠆘󠇙󠆝󠅵󠇗󠆭󠆁󠄐󠇗󠅹󠅸󠇖󠆍󠅳󠇖󠅹󠅰󠇖󠆌󠅹󠄬󠅒󠅢󠄟󠄮
作者信息:黄治军,易卫东,韩荣东,王瑞敏(武汉钢铁有限公司,湖北武汉430080)󠄐󠄹󠅀󠄪󠄢󠄡󠄦󠄞󠄧󠄣󠄞󠄢󠄡󠄦󠄞󠄡󠄡󠄠󠄬󠅒󠅢󠄟󠄮󠄐󠅅󠄹󠄴󠄪󠄾󠅟󠅤󠄐󠄼󠅟󠅗󠅙󠅞󠄬󠅒󠅢󠄟󠄮󠇘󠆭󠆘󠇙󠆝󠅵󠇗󠆭󠆁󠄐󠇗󠅹󠅸󠇖󠆍󠅳󠇖󠅹󠅰󠇖󠆌󠅹󠄬󠅒󠅢󠄟󠄮
期刊信息:《电焊机》 2018年第8期󠄐󠄹󠅀󠄪󠄢󠄡󠄦󠄞󠄧󠄣󠄞󠄢󠄡󠄦󠄞󠄡󠄡󠄠󠄬󠅒󠅢󠄟󠄮󠄐󠅅󠄹󠄴󠄪󠄾󠅟󠅤󠄐󠄼󠅟󠅗󠅙󠅞󠄬󠅒󠅢󠄟󠄮󠇘󠆭󠆘󠇙󠆝󠅵󠇗󠆭󠆁󠄐󠇗󠅹󠅸󠇖󠆍󠅳󠇖󠅹󠅰󠇖󠆌󠅹󠄬󠅒󠅢󠄟󠄮