轨距精调是减少列车左右摆动,减少蛇形晃车、减少列车轮对对轨道结构冲击的有效手段。学者周太平等[1]认为:高速铁路轨道精测精调作业影响因素较多,人员的操作水平和熟练程度、仪器设备的状态以及外界均可对测量结果产生影响,在高速铁路的施工和日常保养维护过程中,应严格组织作业人员进行培训和技术交流,学习高速铁路相关规范,严格按照作业流程和注意事项进行作业,以提高线路的高平顺性和高稳定性,这将直接保障列车的运行安全和提高旅客的舒适性。学者孟永福认为:轨距精度提高的同时,尽量采用正轨距,减少车轮与轨道的撞击。󠄐󠄹󠅀󠄪󠄢󠄡󠄦󠄞󠄧󠄣󠄞󠄢󠄡󠄦󠄞󠄡󠄡󠄠󠄬󠅒󠅢󠄟󠄮󠄐󠅅󠄹󠄴󠄪󠄾󠅟󠅤󠄐󠄼󠅟󠅗󠅙󠅞󠄬󠅒󠅢󠄟󠄮󠇘󠆭󠆘󠇙󠆝󠅵󠇗󠆭󠆁󠄐󠇗󠅹󠅸󠇖󠆍󠅳󠇖󠅹󠅰󠇖󠆌󠅹󠄬󠅒󠅢󠄟󠄮
学者刘志森认为:轨道精调是确保线路质量的重要环节,轨距精调是轨道精调中不可或缺的质量控制工序。通过对轨距进行调整,使轨距正确,扣件齐全,螺栓扭矩、扣件压力合格,达到大机精细捣固的作业条件。轨距精调是大型捣固机作业质量保证的重要条件。学者戴宗林认为:人工轨距精调主要解决轨距不良及不平顺,弥补大机捣固无法改善轨距缺陷的缺点,为避免作业互相干扰,保证各组作业安全,大机捣固与人工精调作业可分区间作业。󠄐󠄹󠅀󠄪󠄢󠄡󠄦󠄞󠄧󠄣󠄞󠄢󠄡󠄦󠄞󠄡󠄡󠄠󠄬󠅒󠅢󠄟󠄮󠄐󠅅󠄹󠄴󠄪󠄾󠅟󠅤󠄐󠄼󠅟󠅗󠅙󠅞󠄬󠅒󠅢󠄟󠄮󠇘󠆭󠆘󠇙󠆝󠅵󠇗󠆭󠆁󠄐󠇗󠅹󠅸󠇖󠆍󠅳󠇖󠅹󠅰󠇖󠆌󠅹󠄬󠅒󠅢󠄟󠄮
1 合武高铁FC 型扣件系统介绍
合武高铁FC 型轨道扣件系统,是我国在高速铁路上首次引进应用成熟的有砟轨道扣件系统。大别山隧道内采用无砟SFC 系统,其他地段采用FC 扣件系统。
FC 型扣件系统为无螺栓无挡肩扣件,具有联结零部件少,结构紧凑,保持轨距能力强,快速安装和拆卸,养护维修成本较低。在Ⅲa 轨枕时预先埋设底座,弹条通过插入预埋底座直接扣压钢轨。预埋底座与钢轨间设有绝缘轨距块,通过更换绝缘轨距块实现钢轨左右位置的调整。󠄐󠄹󠅀󠄪󠄢󠄡󠄦󠄞󠄧󠄣󠄞󠄢󠄡󠄦󠄞󠄡󠄡󠄠󠄬󠅒󠅢󠄟󠄮󠄐󠅅󠄹󠄴󠄪󠄾󠅟󠅤󠄐󠄼󠅟󠅗󠅙󠅞󠄬󠅒󠅢󠄟󠄮󠇘󠆭󠆘󠇙󠆝󠅵󠇗󠆭󠆁󠄐󠇗󠅹󠅸󠇖󠆍󠅳󠇖󠅹󠅰󠇖󠆌󠅹󠄬󠅒󠅢󠄟󠄮
该扣件不能通过更换轨下垫板厚度进行钢轨高低调整,只能通过捣固实现高低调整。󠄐󠄹󠅀󠄪󠄢󠄡󠄦󠄞󠄧󠄣󠄞󠄢󠄡󠄦󠄞󠄡󠄡󠄠󠄬󠅒󠅢󠄟󠄮󠄐󠅅󠄹󠄴󠄪󠄾󠅟󠅤󠄐󠄼󠅟󠅗󠅙󠅞󠄬󠅒󠅢󠄟󠄮󠇘󠆭󠆘󠇙󠆝󠅵󠇗󠆭󠆁󠄐󠇗󠅹󠅸󠇖󠆍󠅳󠇖󠅹󠅰󠇖󠆌󠅹󠄬󠅒󠅢󠄟󠄮
标准配置的FC 型扣件系统由弹条、绝缘帽、轨距挡块、轨下垫板和预埋底座组成,如图1 所示。󠄐󠄹󠅀󠄪󠄢󠄡󠄦󠄞󠄧󠄣󠄞󠄢󠄡󠄦󠄞󠄡󠄡󠄠󠄬󠅒󠅢󠄟󠄮󠄐󠅅󠄹󠄴󠄪󠄾󠅟󠅤󠄐󠄼󠅟󠅗󠅙󠅞󠄬󠅒󠅢󠄟󠄮󠇘󠆭󠆘󠇙󠆝󠅵󠇗󠆭󠆁󠄐󠇗󠅹󠅸󠇖󠆍󠅳󠇖󠅹󠅰󠇖󠆌󠅹󠄬󠅒󠅢󠄟󠄮
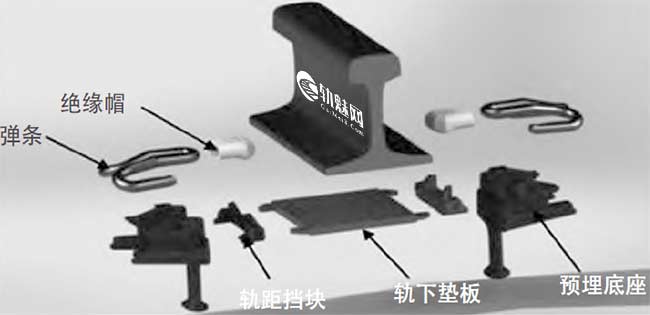
图1 FC型扣件系统
预埋底座在IIIa 轨枕出厂时已经预埋在轨枕上。标准配置时钢轨外侧安装10mm 轨距挡块,钢轨内侧安装11mm 轨距挡块;通过更换不同厚度的轨距挡块,可以实现-8~+8mm 的轨距调整范围。
2 合武高铁轨距精调的现状和难题
2.1 合武高铁轨距精调的现状
2.1.1 作业流程繁琐
高铁轨距精调作业流程复杂,从前期作业准备轨距精调地点的选取到精调区段测量及精调方案的制定,作业前工机具、材料准备,现场作业人员的分工,作业中各个环节节点的卡控,作业后轨距材料和机具的回收、清场、作业质量回检,确认放行列车条件以及后期动静态质量评定等,要求作业流程必须明确、工作细致。󠄐󠄹󠅀󠄪󠄢󠄡󠄦󠄞󠄧󠄣󠄞󠄢󠄡󠄦󠄞󠄡󠄡󠄠󠄬󠅒󠅢󠄟󠄮󠄐󠅅󠄹󠄴󠄪󠄾󠅟󠅤󠄐󠄼󠅟󠅗󠅙󠅞󠄬󠅒󠅢󠄟󠄮󠇘󠆭󠆘󠇙󠆝󠅵󠇗󠆭󠆁󠄐󠇗󠅹󠅸󠇖󠆍󠅳󠇖󠅹󠅰󠇖󠆌󠅹󠄬󠅒󠅢󠄟󠄮
2.1.2 现场技术标准要求严格
高铁对轨距精调的技术标准要求高,作业标准严格,为确保动车组和旅客人员的绝对安全,作业后的几何尺寸各项峰值必须在静态几何尺寸作业验收容许偏差管理值之内,同时现场精调后的轨距要达到-0.5~0 mm 的标准;现场负责人检查复核几何尺寸满足开通条件后,才能确保线路开通后动车组安全运行。󠄐󠄹󠅀󠄪󠄢󠄡󠄦󠄞󠄧󠄣󠄞󠄢󠄡󠄦󠄞󠄡󠄡󠄠󠄬󠅒󠅢󠄟󠄮󠄐󠅅󠄹󠄴󠄪󠄾󠅟󠅤󠄐󠄼󠅟󠅗󠅙󠅞󠄬󠅒󠅢󠄟󠄮󠇘󠆭󠆘󠇙󠆝󠅵󠇗󠆭󠆁󠄐󠇗󠅹󠅸󠇖󠆍󠅳󠇖󠅹󠅰󠇖󠆌󠅹󠄬󠅒󠅢󠄟󠄮
2.1.3 夜间作业
高铁维修天窗根据运行图动车组开行情况确定的,一般利用00:00 至次日04:00 时间段进行维修作业,夜间作业视线条件差,时间紧,有时V 形天窗还需注意邻线上运行的车辆,作业风险较高,同时本次天窗结束至第二个夜间天窗开始,线路要确保高密度动车组运行畅通。󠄐󠄹󠅀󠄪󠄢󠄡󠄦󠄞󠄧󠄣󠄞󠄢󠄡󠄦󠄞󠄡󠄡󠄠󠄬󠅒󠅢󠄟󠄮󠄐󠅅󠄹󠄴󠄪󠄾󠅟󠅤󠄐󠄼󠅟󠅗󠅙󠅞󠄬󠅒󠅢󠄟󠄮󠇘󠆭󠆘󠇙󠆝󠅵󠇗󠆭󠆁󠄐󠇗󠅹󠅸󠇖󠆍󠅳󠇖󠅹󠅰󠇖󠆌󠅹󠄬󠅒󠅢󠄟󠄮
2.1.4 现场人机物管控风险大
轨道精调作业人员分散、作业工机具、材料多,导致现场安全管理难度大,作业组织要求高,必须严格落实由作业负责人进行几何尺寸质量回检,落实记名检、记名修、旧料回收确认等工作,达到列车放行条件后,经负责人检查,确认所有人员、机具、材料已全部下道至封闭栅栏网外后,下达撤除防护作业命令,通知驻站防护员施工结束,办理登销记手续方可开通线路。󠄐󠄹󠅀󠄪󠄢󠄡󠄦󠄞󠄧󠄣󠄞󠄢󠄡󠄦󠄞󠄡󠄡󠄠󠄬󠅒󠅢󠄟󠄮󠄐󠅅󠄹󠄴󠄪󠄾󠅟󠅤󠄐󠄼󠅟󠅗󠅙󠅞󠄬󠅒󠅢󠄟󠄮󠇘󠆭󠆘󠇙󠆝󠅵󠇗󠆭󠆁󠄐󠇗󠅹󠅸󠇖󠆍󠅳󠇖󠅹󠅰󠇖󠆌󠅹󠄬󠅒󠅢󠄟󠄮
2.2 合武高铁轨距精调的难点
2.2.1 传统的轨距精调作业模式
长期采用综合检测列车波形图分析点状轨距不良地段调整的作业模式,通过调整单股轨距-0.3~0.3 mm 范围内,未调整轨向、未消除轨距块与轨底间离缝,这种作业模式不仅效率低下,而且作业效果差,轨距TQI 变化幅值不明显,甚至出现多个地段调整后轨距TQI 不降反升的情况。󠄐󠄹󠅀󠄪󠄢󠄡󠄦󠄞󠄧󠄣󠄞󠄢󠄡󠄦󠄞󠄡󠄡󠄠󠄬󠅒󠅢󠄟󠄮󠄐󠅅󠄹󠄴󠄪󠄾󠅟󠅤󠄐󠄼󠅟󠅗󠅙󠅞󠄬󠅒󠅢󠄟󠄮󠇘󠆭󠆘󠇙󠆝󠅵󠇗󠆭󠆁󠄐󠇗󠅹󠅸󠇖󠆍󠅳󠇖󠅹󠅰󠇖󠆌󠅹󠄬󠅒󠅢󠄟󠄮
2.2.2 扣件系统失效
合武高铁扣件是2008 年铺设上道使用的,到2023年已经服役达15 年,上下行通过总重达180MT。使用年限长,扣件系统出现了不同的伤损,扣件扣压力衰减严重,同时出现弹条断裂、绝缘顶帽破损,弹条防锈涂层龟裂脱落,弹条金属表面存在锈蚀凹坑,塑性变形无法恢复。随机抽取100 件样品送检测试扣压力性能,测试结果显示,100 件弹条样品中40 件弹条扣压力满足设计要求,其余60 件弹条扣压力低于设计要求,最大偏差-8.55%。󠄐󠄹󠅀󠄪󠄢󠄡󠄦󠄞󠄧󠄣󠄞󠄢󠄡󠄦󠄞󠄡󠄡󠄠󠄬󠅒󠅢󠄟󠄮󠄐󠅅󠄹󠄴󠄪󠄾󠅟󠅤󠄐󠄼󠅟󠅗󠅙󠅞󠄬󠅒󠅢󠄟󠄮󠇘󠆭󠆘󠇙󠆝󠅵󠇗󠆭󠆁󠄐󠇗󠅹󠅸󠇖󠆍󠅳󠇖󠅹󠅰󠇖󠆌󠅹󠄬󠅒󠅢󠄟󠄮
2.2.3 人身安全管控风险较大
现场作业按照流程分工进行,有检查划撬,更换弹条,操控改道器,调整轨距块,消除离缝,旧料回收,质量回检等多个环节,多小组联合作业,人员较多,工作地点较为分散,需要对现场人员、作业机具严格管理卡控,落实“当日干、当日验、当日清”要求才能确保作业现场人员的人身安全。󠄐󠄹󠅀󠄪󠄢󠄡󠄦󠄞󠄧󠄣󠄞󠄢󠄡󠄦󠄞󠄡󠄡󠄠󠄬󠅒󠅢󠄟󠄮󠄐󠅅󠄹󠄴󠄪󠄾󠅟󠅤󠄐󠄼󠅟󠅗󠅙󠅞󠄬󠅒󠅢󠄟󠄮󠇘󠆭󠆘󠇙󠆝󠅵󠇗󠆭󠆁󠄐󠇗󠅹󠅸󠇖󠆍󠅳󠇖󠅹󠅰󠇖󠆌󠅹󠄬󠅒󠅢󠄟󠄮
2.2.4 缺少作业后动静态质量评定
作业后对轨距的动态、静态的评定是对轨距精调的持续改进,提升作业质量的闭环作业管理的重要手段,以往由于受作业单位缺少专业人员、施工任务多等客观条件限制,很难完成,缺少监管。利用设备周期检查结合0 级轨道检查仪、综合检测列车数据对轨距精调地段的精调质量进行复核,对轨距TQI 值上升的区段追根溯源,查找出轨距精调项目和日常维修作业造成几何尺寸变化的原因,有效延长作业质量,严控作业标准的质量评定势在必行。󠄐󠄹󠅀󠄪󠄢󠄡󠄦󠄞󠄧󠄣󠄞󠄢󠄡󠄦󠄞󠄡󠄡󠄠󠄬󠅒󠅢󠄟󠄮󠄐󠅅󠄹󠄴󠄪󠄾󠅟󠅤󠄐󠄼󠅟󠅗󠅙󠅞󠄬󠅒󠅢󠄟󠄮󠇘󠆭󠆘󠇙󠆝󠅵󠇗󠆭󠆁󠄐󠇗󠅹󠅸󠇖󠆍󠅳󠇖󠅹󠅰󠇖󠆌󠅹󠄬󠅒󠅢󠄟󠄮
3 轨距精调难题的解决办法
3.1 突破传统的作业模式
现场调研发现,传统的轨距精调作业模式已经不能适应现阶段高速铁路对几何尺寸平顺性要求,必须突破原有固化的轨距精调模式,采取更加合理有效的方式优化轨距精调的作业手段,采取开会讨论、现场试点、数据对比分析的方法,找准适合合武高铁FC 扣件的轨距精调的作业模式。
3.1.1 精调地点的选取
第一步通过对综合检测列车波形图分析出轨距不平顺地段,结合轨距TQI 区段表和波形图实际情况查照,以1 km 为一个单元进行轨距精调作业,并结合TQI 计算公式,当轨距几何偏差在单元区段中连续采样点的幅值无突变大值时,轨距TQI 的数值才会降低,合武高铁1 km平均轨距超出0.6mm 的区段有172 处,占总单元数(250个单元) 的68.8%,因此选取1 km 单元区段平均轨距TQI>0.6mm 的地段进行测量。
$$TQI=\sum_{i=1}^{7}\sigma _i \qquad (公式1)$$󠄐󠄹󠅀󠄪󠄢󠄡󠄦󠄞󠄧󠄣󠄞󠄢󠄡󠄦󠄞󠄡󠄡󠄠󠄬󠅒󠅢󠄟󠄮󠄐󠅅󠄹󠄴󠄪󠄾󠅟󠅤󠄐󠄼󠅟󠅗󠅙󠅞󠄬󠅒󠅢󠄟󠄮󠇘󠆭󠆘󠇙󠆝󠅵󠇗󠆭󠆁󠄐󠇗󠅹󠅸󠇖󠆍󠅳󠇖󠅹󠅰󠇖󠆌󠅹󠄬󠅒󠅢󠄟󠄮
$$\sigma _i=\sqrt{\frac{1}{n}\sum_{j=1}^{n}\left ( X_{ij}-\bar{X}_i\right )^2} \qquad (公式2)$$󠄐󠄹󠅀󠄪󠄢󠄡󠄦󠄞󠄧󠄣󠄞󠄢󠄡󠄦󠄞󠄡󠄡󠄠󠄬󠅒󠅢󠄟󠄮󠄐󠅅󠄹󠄴󠄪󠄾󠅟󠅤󠄐󠄼󠅟󠅗󠅙󠅞󠄬󠅒󠅢󠄟󠄮󠇘󠆭󠆘󠇙󠆝󠅵󠇗󠆭󠆁󠄐󠇗󠅹󠅸󠇖󠆍󠅳󠇖󠅹󠅰󠇖󠆌󠅹󠄬󠅒󠅢󠄟󠄮
$$\bar{X}_i=\frac{1}{n}\sum_{j=1}^{n}X_{ij} \qquad (公式3)$$󠄐󠄹󠅀󠄪󠄢󠄡󠄦󠄞󠄧󠄣󠄞󠄢󠄡󠄦󠄞󠄡󠄡󠄠󠄬󠅒󠅢󠄟󠄮󠄐󠅅󠄹󠄴󠄪󠄾󠅟󠅤󠄐󠄼󠅟󠅗󠅙󠅞󠄬󠅒󠅢󠄟󠄮󠇘󠆭󠆘󠇙󠆝󠅵󠇗󠆭󠆁󠄐󠇗󠅹󠅸󠇖󠆍󠅳󠇖󠅹󠅰󠇖󠆌󠅹󠄬󠅒󠅢󠄟󠄮
\(\sigma _i\)为各项几何偏差的标准差;\(i=1,2, \cdots ,7\);分别为左高低、右高低、左轨向、右轨向、轨距、水平和三角坑。󠄐󠄹󠅀󠄪󠄢󠄡󠄦󠄞󠄧󠄣󠄞󠄢󠄡󠄦󠄞󠄡󠄡󠄠󠄬󠅒󠅢󠄟󠄮󠄐󠅅󠄹󠄴󠄪󠄾󠅟󠅤󠄐󠄼󠅟󠅗󠅙󠅞󠄬󠅒󠅢󠄟󠄮󠇘󠆭󠆘󠇙󠆝󠅵󠇗󠆭󠆁󠄐󠇗󠅹󠅸󠇖󠆍󠅳󠇖󠅹󠅰󠇖󠆌󠅹󠄬󠅒󠅢󠄟󠄮
\(X _{ij}\)是指在200m单元区段中各项几何偏差的幅值;\(j=1,2, \cdots ,n;i=1,2, \cdots ,7\)。󠄐󠄹󠅀󠄪󠄢󠄡󠄦󠄞󠄧󠄣󠄞󠄢󠄡󠄦󠄞󠄡󠄡󠄠󠄬󠅒󠅢󠄟󠄮󠄐󠅅󠄹󠄴󠄪󠄾󠅟󠅤󠄐󠄼󠅟󠅗󠅙󠅞󠄬󠅒󠅢󠄟󠄮󠇘󠆭󠆘󠇙󠆝󠅵󠇗󠆭󠆁󠄐󠇗󠅹󠅸󠇖󠆍󠅳󠇖󠅹󠅰󠇖󠆌󠅹󠄬󠅒󠅢󠄟󠄮
n是采样点的个数(200m单元区段中每隔0.25米采集一个点,n=800)。󠄐󠄹󠅀󠄪󠄢󠄡󠄦󠄞󠄧󠄣󠄞󠄢󠄡󠄦󠄞󠄡󠄡󠄠󠄬󠅒󠅢󠄟󠄮󠄐󠅅󠄹󠄴󠄪󠄾󠅟󠅤󠄐󠄼󠅟󠅗󠅙󠅞󠄬󠅒󠅢󠄟󠄮󠇘󠆭󠆘󠇙󠆝󠅵󠇗󠆭󠆁󠄐󠇗󠅹󠅸󠇖󠆍󠅳󠇖󠅹󠅰󠇖󠆌󠅹󠄬󠅒󠅢󠄟󠄮
第二步采用0 级轨道检查仪对单元区段平均轨距TQI>0.6mm 的地段进行静态测量,为了使精测和精调里程一致,提前利用轨道检查仪和CPⅢ点对线路里程进行拉链标定。测量前需在0 级轨道检查仪的计算机上提前编辑出测量地段的轨枕号,现场每20 米在轨枕上用油漆标定具体轨枕号,结合拉链的里程核对一次里程误差,现场使用10m 弦长进行测量,减小0 级轨道检查仪带来的系统误差,提高轨道检查仪测量数据精确度,确保精调作业的信息化和标准化,提高后期作业质量和效率。󠄐󠄹󠅀󠄪󠄢󠄡󠄦󠄞󠄧󠄣󠄞󠄢󠄡󠄦󠄞󠄡󠄡󠄠󠄬󠅒󠅢󠄟󠄮󠄐󠅅󠄹󠄴󠄪󠄾󠅟󠅤󠄐󠄼󠅟󠅗󠅙󠅞󠄬󠅒󠅢󠄟󠄮󠇘󠆭󠆘󠇙󠆝󠅵󠇗󠆭󠆁󠄐󠇗󠅹󠅸󠇖󠆍󠅳󠇖󠅹󠅰󠇖󠆌󠅹󠄬󠅒󠅢󠄟󠄮
3.1.3 轨距精调方案的制定
第三步轨距精调方案的制定,重在线型拟合,根据测量数据拟定一个精调后的轨距和轨向TQI 的静态目标值,利用试算软件计算出每根轨枕的调整量,按照先轨向后轨距的调整原则,结合现场轨距块11mm、12mm 的数量制定出轨距精调方案。轨距精调方案制定后,请经验丰富的师傅进行现场复核,针对精调方案进行小范围区段分级处理。处理的原则为轨距和轨向TQI≥±0.5mm 的数值优先处理,TQI<±0.5mm 的数值暂缓处理。󠄐󠄹󠅀󠄪󠄢󠄡󠄦󠄞󠄧󠄣󠄞󠄢󠄡󠄦󠄞󠄡󠄡󠄠󠄬󠅒󠅢󠄟󠄮󠄐󠅅󠄹󠄴󠄪󠄾󠅟󠅤󠄐󠄼󠅟󠅗󠅙󠅞󠄬󠅒󠅢󠄟󠄮󠇘󠆭󠆘󠇙󠆝󠅵󠇗󠆭󠆁󠄐󠇗󠅹󠅸󠇖󠆍󠅳󠇖󠅹󠅰󠇖󠆌󠅹󠄬󠅒󠅢󠄟󠄮
3.1.4 调整现场精调作业模式
第四步调整现场精调作业模式,方案制定是现场轨距精调的理论支撑,现场作业需按照测量地点和精调量进行实施,现场作业要根据实际情况,如轨距块的使用情况、弹条的锈蚀情况、轨枕的偏斜等多方面因素进行综合考虑后进行调整。󠄐󠄹󠅀󠄪󠄢󠄡󠄦󠄞󠄧󠄣󠄞󠄢󠄡󠄦󠄞󠄡󠄡󠄠󠄬󠅒󠅢󠄟󠄮󠄐󠅅󠄹󠄴󠄪󠄾󠅟󠅤󠄐󠄼󠅟󠅗󠅙󠅞󠄬󠅒󠅢󠄟󠄮󠇘󠆭󠆘󠇙󠆝󠅵󠇗󠆭󠆁󠄐󠇗󠅹󠅸󠇖󠆍󠅳󠇖󠅹󠅰󠇖󠆌󠅹󠄬󠅒󠅢󠄟󠄮
试验段选在合武高铁下行K745+600 至K746+600精调前轨距TQI=0.62mm,精调后轨距TQI=0.26 mm,下降幅值58%,实现了轨距TQI≤0.3mm 的新目标。轨距精调评定后,结论为质保期长,反弹幅度小。实践证明,具有可行性和有效性。󠄐󠄹󠅀󠄪󠄢󠄡󠄦󠄞󠄧󠄣󠄞󠄢󠄡󠄦󠄞󠄡󠄡󠄠󠄬󠅒󠅢󠄟󠄮󠄐󠅅󠄹󠄴󠄪󠄾󠅟󠅤󠄐󠄼󠅟󠅗󠅙󠅞󠄬󠅒󠅢󠄟󠄮󠇘󠆭󠆘󠇙󠆝󠅵󠇗󠆭󠆁󠄐󠇗󠅹󠅸󠇖󠆍󠅳󠇖󠅹󠅰󠇖󠆌󠅹󠄬󠅒󠅢󠄟󠄮
3.2 整治失效扣件系统
高速铁路系统的高安全性、可靠性、平顺性对高速铁路的扣件系统提出更高的要求,扣件系统需长期保持轨距的能力,具有更高防爬阻力,联结零件少,养护工作量少的特点,同时具备更好的减振和更高的绝缘性能。
3.3 合理调整人员分工
轨距精调人员根据作业任务相对固定,按照作业地点和时间节点进行分工,利用班前会和施工专项会议进行安全风险预知训练教育和作业风险研判。
3.4 加强现场工具和材料管理
设立专人对每日上道的工具和材料进行分类清点登记,在出库前、进网前、出网前和入库前进行清点,保证没有工具和材料遗留在线路上,做好台账登记,动态更新,严格管理。
3.5 严控作业效果质量评定
制定轨距精调专项达标标准及奖惩标准,明确奖罚标准,作业后地段轨距TQI 目标管理值小于等于0.3mm,下降幅值大于等于30%,评定为合格。优于这个指标的进行奖励。
4 优化后的轨距精调模式
4.1 轨距精调调查准备工作
根据综合检测列车《轨道质量指数(TQI)报告表》优先选取单项轨距TQI≥0.6mm 的连续地段,每单元长度原则上不少于1 km,200m 的整倍数,提高静态测量的效率,确保轨距精调的完整性,提高后续数据符合的追踪性。结合设备综合台账分析波形图里程误差的校核,减少现场精调作业地点的误差,并通过综合检测列车的多次波形图轨距项目变化趋势,进行截图保存,为后续数据追踪做好准备,并建立台账。检查工区负责综合检测列车波形图图纸里程误差的校正工作,根据综合检测列车波形图特征点(如区间的曲线要素点)和岔区的道岔尖轨台账里程进行校核,并提前在0 级轨道检查仪系统上编辑出需测量地段的轨枕号。现场校核轨道检查仪轨距和水平项目,其中一人根据已确定后的拉链里程起始点逐枕测量;2 人跟随轨道检查仪,在两股钢轨上逐枕检查轨道结构病害并标记在轨枕上;另一人,负责每20 m 标注一处轨枕号。
4.2 轨道数据测量
在0 级轨道检查仪上核对设计线形资料,确保输入数据与现场和台账相符,重点核对平面直线、曲线要素点位置;纵断面竖曲线要素和边坡点起终点位置,通过轨道检查仪双轮确定测量基准股。轨距精调前安排专任对拟精调地段进行扣件系统调查,把弹条扣压力不足、弹条变形、扣件锈蚀失效,钢轨肥边、掉块、不均匀磨耗等情况调查出来,在扣件失效的轨距块的轨枕上标注“–”,需要更换弹条和需要改锚的轨枕上标注“X”。按照轨道检查仪和轨距尺测量对需要精调地点进行精确的测量,测量过程中注意核对轨道检查仪和轨距尺检查数据的吻合性,出现偏差时,及时查照原因,及时修正,测量结束后,及时导出测量数据以便调整和数据进一步分析,做好测量数据的搭接,搭接长度不少于20m。采用线型拟合,根据综合检测列车、现场静态测量和扣件调查情况,确定一个结合调整量的轨道精调后轨距和轨向的TQI 目标值,再对数据异常值,有突变的值结合现场静态测量结果进行修正剔除,按照方案中轨距TQI 分级处理,轨距和轨向TQI≥±0.5 mm 的数值优先处理,TQI<±0.5 mm 的数值暂缓处理。
4.3 管理人员分工
成立轨距精测精调领导小组,由主管生产副段长任组长,负责项目的协调管理工作,保证轨距精调项目顺利进行。
线路技术科主管工程师负责具体项目的实施,轨距精调项目方案制定,协调轨距调整件的计划、落实;督办各精调线路车间任务进度,下发精调进度表,提报段领导各车间轨距精调的落实情况,指导现场作业标准,及时反馈作业现场质量,作业效率,做好验工计价等工作。线路车间生产副主任负责具体轨距精调项目的实施,从任务量调查,人员组织配备,作业质量卡控,放行列车条件确认等各环节做好卡控。段安全生产指挥中心负责作业天窗计划落实,作业进出网工机具的入网、出网的卡控。检查工区负责精调前后动静态数据的对比分析,及时反馈作业后综合检测列车检查数据的对比,对TQI 下降不明显甚至反弹情况及时上报项目领导小组,对作业地段作业项目进行评定。󠄐󠄹󠅀󠄪󠄢󠄡󠄦󠄞󠄧󠄣󠄞󠄢󠄡󠄦󠄞󠄡󠄡󠄠󠄬󠅒󠅢󠄟󠄮󠄐󠅅󠄹󠄴󠄪󠄾󠅟󠅤󠄐󠄼󠅟󠅗󠅙󠅞󠄬󠅒󠅢󠄟󠄮󠇘󠆭󠆘󠇙󠆝󠅵󠇗󠆭󠆁󠄐󠇗󠅹󠅸󠇖󠆍󠅳󠇖󠅹󠅰󠇖󠆌󠅹󠄬󠅒󠅢󠄟󠄮
4.4 作业人员分工
合武高铁轨距精调的人员分工明确,按照不同号位进行分工,明确每个号位岗位职责,按照1#~9# 进行岗位分工,线下模式,待熟练后现场实施,不同号位之间进行工作补充。
1#、2# 负责松卸SF 扣件,利用专用安装拆卸工具将需要更换轨距调整件的弹条拆卸下来。3#、4# 负责将需要调整的轨距调整块更换到位,期间需要利用改道器的,必须使用改道器改道,使用橡胶锤轻敲轨距调整块,确保轨距调整块与预埋铁座密贴,使用电子轨距尺测量轨距是否达标。5#、6#负责使用专用安装工具将弹条复位。7(# 负责人) 负责复核综合检测列车检查的波形图和0 级轨道检查仪检查现场作业精度,结合轨距精调作业情况,复核轨向的状态,对差别较大的,立即返工,并在钢轨内测标注箭头,明确调整件状态。8# 负责现场防护,负责现场无缝线路在作业前、作业中、作业后轨温测量,做好防护工作,确保人身安全,协助确认出网前的作业现场物遗留工机具等。9# 负责驻站防护员,做好天窗命令的登销记,与现场防护员3~5 min 通话一次,邻线有列车运行时,通知作业人员下道避车。󠄐󠄹󠅀󠄪󠄢󠄡󠄦󠄞󠄧󠄣󠄞󠄢󠄡󠄦󠄞󠄡󠄡󠄠󠄬󠅒󠅢󠄟󠄮󠄐󠅅󠄹󠄴󠄪󠄾󠅟󠅤󠄐󠄼󠅟󠅗󠅙󠅞󠄬󠅒󠅢󠄟󠄮󠇘󠆭󠆘󠇙󠆝󠅵󠇗󠆭󠆁󠄐󠇗󠅹󠅸󠇖󠆍󠅳󠇖󠅹󠅰󠇖󠆌󠅹󠄬󠅒󠅢󠄟󠄮
4.5 作业节点卡控
为保证高铁维修质量和不影响高铁运行,对从事高铁维修的各个作业都必须做到各个环节的时间节点卡控,也是提高工作效率的必经之路。轨距精调项目的轨距测量、现场工作量的调查,材料分发、扣件拆卸、作业地点划撬、旧料回收和作业回检等流程必须考虑周全,结合作业通道门位置,合理安排时间,作业效率最大化。
前期准备阶段工作时间分配。前期准备阶段,由检查工区对轨距TQI≥0.6mm 单元区段筛选,并结合台账进行综合分析。组织测量人员对该地段的扣减状态进行调查,一并调查工作量,并在现场轨枕上进行标记轨枕号和结构病害。利用0 级轨道检查仪和电子轨距尺测量数据,制定方案。该阶段在轨距精调前3 天内完成。作业前时间分配。作业前2 小时召开分工对接会,作业前1 小时,作业人员准时到达作业现场封闭栅栏门外集合,清点工机具材料,列队做好安全风险预知训练(KYT)和任务分工,交代现场作业注意事项,核对防护用品、作业机具是否齐全有效。防护员拍照上传至安全生产指挥中心,等待入网命令。作业中时间分配。天窗命令下达后,现场防护员先入网,做好天窗命令登记,确认现场安全后,生产人员、机具、材料有序入网,到达作业地点后布置好照明灯具,按照作业分工各号位有条不紊进行工作,作业负责人核对作业起始地点,作业方案内容,确定好作业基准股,标注作业改道方向。作业时间控制180 min 内完成,最后3 分钟做好收尾,人员机具撤出往外,防护员最后出网并拍照上传,通知驻站防护员销记,开通线路。作业后时间分配。󠄐󠄹󠅀󠄪󠄢󠄡󠄦󠄞󠄧󠄣󠄞󠄢󠄡󠄦󠄞󠄡󠄡󠄠󠄬󠅒󠅢󠄟󠄮󠄐󠅅󠄹󠄴󠄪󠄾󠅟󠅤󠄐󠄼󠅟󠅗󠅙󠅞󠄬󠅒󠅢󠄟󠄮󠇘󠆭󠆘󠇙󠆝󠅵󠇗󠆭󠆁󠄐󠇗󠅹󠅸󠇖󠆍󠅳󠇖󠅹󠅰󠇖󠆌󠅹󠄬󠅒󠅢󠄟󠄮
按照区段作业要求,一般完成轨距精调1 km 作业需要10~12 d,作业结束后尽快在2 d 内完成精调段的质量评定,检查工区分析人员结合最近一次综合检测列车的数据进行动态评定,并将结果上报给段主管人员及段领导,下发轨距精调简报,总结经验,发扬优点,为后续精调做好指导。󠄐󠄹󠅀󠄪󠄢󠄡󠄦󠄞󠄧󠄣󠄞󠄢󠄡󠄦󠄞󠄡󠄡󠄠󠄬󠅒󠅢󠄟󠄮󠄐󠅅󠄹󠄴󠄪󠄾󠅟󠅤󠄐󠄼󠅟󠅗󠅙󠅞󠄬󠅒󠅢󠄟󠄮󠇘󠆭󠆘󠇙󠆝󠅵󠇗󠆭󠆁󠄐󠇗󠅹󠅸󠇖󠆍󠅳󠇖󠅹󠅰󠇖󠆌󠅹󠄬󠅒󠅢󠄟󠄮
4.6 工具清点
高铁作业严格落实工机具三清点制度,数量、类型、状态,出库、进网、出网及入库制度,及时拍照存档,杜绝工机具无计划入网。
5 结束语
目前,已经形成了一套适合合武高铁轨距精调的作业模式和完整的作业流程,经过在现场试用、检验、流程明确和结构优化,证明其可实施性和科学可行性。此项轨距精调方案应用前景广阔,可以广泛应用到其他有砟高铁轨距精调作业,同构综合检测列车检查结果表明,此成果能有效减低轨距和轨向TQI 值,结合大机捣固作业,能有效提高舒适度,延长有砟高铁轨道使用寿命。
我国高铁开行数量的增加和运营年限增加,对线路高平顺性、高可靠性有着更高的要求,人工轨距精调作业结合大型机械捣固,发挥各自优势,提高大型养路机械作业效率,克服人工整治长波病害的难题,提升高铁线路质量和劳动效率。󠄐󠄹󠅀󠄪󠄢󠄡󠄦󠄞󠄧󠄣󠄞󠄢󠄡󠄦󠄞󠄡󠄡󠄠󠄬󠅒󠅢󠄟󠄮󠄐󠅅󠄹󠄴󠄪󠄾󠅟󠅤󠄐󠄼󠅟󠅗󠅙󠅞󠄬󠅒󠅢󠄟󠄮󠇘󠆭󠆘󠇙󠆝󠅵󠇗󠆭󠆁󠄐󠇗󠅹󠅸󠇖󠆍󠅳󠇖󠅹󠅰󠇖󠆌󠅹󠄬󠅒󠅢󠄟󠄮
文章来源:
原文名称:有砟高铁轨距精调的作业模式优化研究󠄐󠄹󠅀󠄪󠄢󠄡󠄦󠄞󠄧󠄣󠄞󠄢󠄡󠄦󠄞󠄡󠄡󠄠󠄬󠅒󠅢󠄟󠄮󠄐󠅅󠄹󠄴󠄪󠄾󠅟󠅤󠄐󠄼󠅟󠅗󠅙󠅞󠄬󠅒󠅢󠄟󠄮󠇘󠆭󠆘󠇙󠆝󠅵󠇗󠆭󠆁󠄐󠇗󠅹󠅸󠇖󠆍󠅳󠇖󠅹󠅰󠇖󠆌󠅹󠄬󠅒󠅢󠄟󠄮
作者信息:曲玉福(武汉铁路职业技术学院,武汉430000)󠄐󠄹󠅀󠄪󠄢󠄡󠄦󠄞󠄧󠄣󠄞󠄢󠄡󠄦󠄞󠄡󠄡󠄠󠄬󠅒󠅢󠄟󠄮󠄐󠅅󠄹󠄴󠄪󠄾󠅟󠅤󠄐󠄼󠅟󠅗󠅙󠅞󠄬󠅒󠅢󠄟󠄮󠇘󠆭󠆘󠇙󠆝󠅵󠇗󠆭󠆁󠄐󠇗󠅹󠅸󠇖󠆍󠅳󠇖󠅹󠅰󠇖󠆌󠅹󠄬󠅒󠅢󠄟󠄮
期刊信息:科技创新与应用 2023 年 29 期󠄐󠄹󠅀󠄪󠄢󠄡󠄦󠄞󠄧󠄣󠄞󠄢󠄡󠄦󠄞󠄡󠄡󠄠󠄬󠅒󠅢󠄟󠄮󠄐󠅅󠄹󠄴󠄪󠄾󠅟󠅤󠄐󠄼󠅟󠅗󠅙󠅞󠄬󠅒󠅢󠄟󠄮󠇘󠆭󠆘󠇙󠆝󠅵󠇗󠆭󠆁󠄐󠇗󠅹󠅸󠇖󠆍󠅳󠇖󠅹󠅰󠇖󠆌󠅹󠄬󠅒󠅢󠄟󠄮
👍👍👍