一、基本概念
全面质量管理(Total Quality Management, TQM)是在最经济的水平上,考虑到充分满足顾客要求的条件下,进行市场研究、设计、制造和售后服务,在企业内各部门中开展开发质量、维持质量及提高质量的活动,构成为一体的一种有效体系。
二、TQM发展史(质量管理发展历经五个阶段)
1. 操作者控制阶段:特点是产品工序一人完成。典型表现是手工作坊。
2. 专人控制阶段:特点是开始由班组长控制产品质量,之后是检验员。代表人物是泰勒(科学管理之父)。20世纪初泰勒提出“科学管理活动”,将计划与执行职能分开并加入检验环节,“工长的质量管理”后演变为检验员的质量管理。
3. 统计控制阶段:特点是制程管制,用统计手段来控制。代表人物是修哈特(SQC之父),1924年休哈特提出控制和预防缺陷概念,创造“控制图”,1925年提出SPC理论,1929 – 1930年道奇和罗米克发表相关论文,提出统计抽样检验方法。
4. 全面质量管理阶段:特点是对所有过程进行管制。代表人物是(费根堡姆(全面质量控制之父)、戴明(质量改进之父)、克劳士比(零缺陷之父)),费根堡姆提出“质量保证”概念,戴明提出PDCA,克劳士比提出零缺陷。
5. 卓越质量管理阶段:特点通过设计、管理和改进达到竞争力的质量水平,代表人物是朱兰(质量领域首席架构师)、石川馨(QCC之父)、狩野纪昭(二位质量之父)、比尔史密斯(西格玛之父),朱兰提出“质量改进三部曲”(质量计划、质量控制和质量改进),石川馨提出QCC,狩野纪昭提出Kano模型,比尔史密斯提出六西格玛。
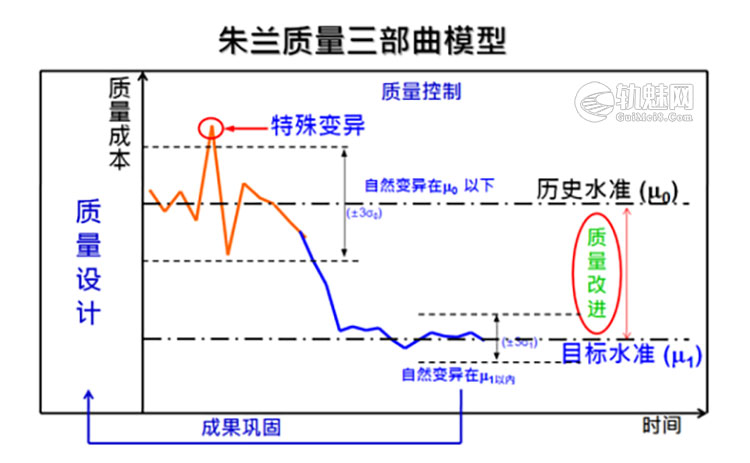
三、TQM的理念
1.核心理念:质量是企业的生命线
TQM的核心思想是“质量第一”,强调质量不是企业中某个部门或环节的职责,而是整个组织的共同使命。其目标是通过全员参与和全过程管理,将质量意识融入企业文化的血液中,最终达到零事故、零缺陷、零故障的目标,实现客户满意、成本降低和效率提升的共赢。󠄐󠄹󠅀󠄪󠄢󠄡󠄦󠄞󠄧󠄣󠄞󠄢󠄡󠄦󠄞󠄤󠄢󠄬󠅒󠅢󠄟󠄮󠄐󠅅󠄹󠄴󠄪󠄾󠅟󠅤󠄐󠄼󠅟󠅗󠅙󠅞󠄬󠅒󠅢󠄟󠄮󠇘󠆭󠆘󠇙󠆝󠅵󠇗󠆭󠆁󠄐󠇗󠅹󠅸󠇖󠆍󠅳󠇖󠅹󠅰󠇖󠆌󠅹󠄬󠅒󠅢󠄟󠄮
2.文化变革:从“事后检验”到“事前预防”
TQM颠覆了传统的“事后检验”模式,主张通过流程优化和缺陷预防,将质量问题消灭在萌芽阶段。例如,戴明(W. Edwards Deming)提出的“质量管理14条原则”中,明确反对依赖最终检验来保证质量。󠄐󠄹󠅀󠄪󠄢󠄡󠄦󠄞󠄧󠄣󠄞󠄢󠄡󠄦󠄞󠄤󠄢󠄬󠅒󠅢󠄟󠄮󠄐󠅅󠄹󠄴󠄪󠄾󠅟󠅤󠄐󠄼󠅟󠅗󠅙󠅞󠄬󠅒󠅢󠄟󠄮󠇘󠆭󠆘󠇙󠆝󠅵󠇗󠆭󠆁󠄐󠇗󠅹󠅸󠇖󠆍󠅳󠇖󠅹󠅰󠇖󠆌󠅹󠄬󠅒󠅢󠄟󠄮
四、TQM框架
五、精益领导范式
精益质量范式参考
序号 | 传统质量范式 | 精益质量范式 | 范式转变 |
范式#01 | 质量控制重点在“事后把关” | 质量控制重点在“过程控制” | 从事后检验到过程控制 |
范式#02 | 关注合格品,合格率达标即认为质量良好 | 关注不合格品,认真对待每一个不合格品 | 从忽视缺陷到调查缺陷 |
范式#03 | 质量问题不可避免 | 质量问题可以避免,关键在于标准的识别、执行与持续改进 | 从接受缺陷到预防缺陷 |
范式#04 | 出现不合格后返工、返修即可 | 出现不合格后,要考虑如何预防 | 从返修到预防 |
范式#05 | 要做好品质,就要增加检验员 | 要做好品质,就要减少对检验的依赖,要防错 | 从依赖检验到内建质量 |
范式#06 | 质量是检验员的事,不关我事 | 人人都是检验员,人人都要对质量负责 | 从孤立责任到共同责任 |
范式#07 | 质量信息分散,记录在纸质台账 | 建立数字化、透明共享的质量信息平台 | 从信息孤岛到信息共享 |
范式#08 | 解决质量问题依靠经验和试错 | 解决质量问题依靠数据分析和科学试验 | 从经验判断到数据驱动 |
范式#09 | 质量问题无法预测,对突发故障只能事后抢修 | 质量问题可以预测,建立动态监测系统,提前采取预防措施 | 从被动响应到主动预防 |
范式#10 | 质量改善是质量部门的职责 | 质量改善需要所有相关部门共同参与 | 从部门分割到跨部门协同 |
- 行为验证九宫格
时间、PDCA、全员参与、无借口、安全、反省、目视、标准、改善
- 四大意识
客户意识、实事求是、利他、用数据说话
第一部分:质量基石
一、标准作业:
定义:
1.流程 2.节拍 3.作业平衡 4.作业序列/布局 5.标准作业书 6.持续性 7.改善󠄐󠄹󠅀󠄪󠄢󠄡󠄦󠄞󠄧󠄣󠄞󠄢󠄡󠄦󠄞󠄤󠄢󠄬󠅒󠅢󠄟󠄮󠄐󠅅󠄹󠄴󠄪󠄾󠅟󠅤󠄐󠄼󠅟󠅗󠅙󠅞󠄬󠅒󠅢󠄟󠄮󠇘󠆭󠆘󠇙󠆝󠅵󠇗󠆭󠆁󠄐󠇗󠅹󠅸󠇖󠆍󠅳󠇖󠅹󠅰󠇖󠆌󠅹󠄬󠅒󠅢󠄟󠄮
标准作业是采用最佳的作业序列,并最好地利用人、机器、工具和材料去完成工作, 然后发展成标准工作流程让所有人遵守。󠄐󠄹󠅀󠄪󠄢󠄡󠄦󠄞󠄧󠄣󠄞󠄢󠄡󠄦󠄞󠄤󠄢󠄬󠅒󠅢󠄟󠄮󠄐󠅅󠄹󠄴󠄪󠄾󠅟󠅤󠄐󠄼󠅟󠅗󠅙󠅞󠄬󠅒󠅢󠄟󠄮󠇘󠆭󠆘󠇙󠆝󠅵󠇗󠆭󠆁󠄐󠇗󠅹󠅸󠇖󠆍󠅳󠇖󠅹󠅰󠇖󠆌󠅹󠄬󠅒󠅢󠄟󠄮
作用:消除疑问点的教育方法,主要以疑问点为中心进行教育。
案例:作业指导书及修订
二、JI工作教导-教三练四:
工作教导定义:英文原意:在企业内部(不脱产)的培训;日本译为:现场督导者技能训练;中文译为:一线主管技能训练
教三练四步骤:
教三:
- 第一遍:老师一边演示,一边说步骤
- 第二遍:老师一边演示,一边说步骤及要点
- 第三遍:老师一边演示,一边说步骤、要点及理由
练四:
- 第一遍:学员尝试完整操作,但不用解说
- 第二遍:学员一边做,一边说出主要步骤
- 第三遍:学员一边做,一边说出主要步骤和要点
- 第四遍:学员一边做,一边说出主要步骤、要点及理由
三、OPL单点课程:
定义:是指把一个项目(点)在一张纸上按标准格式进行整理后,以小组组员为对象进行5~10分钟的教育。
要求:80%图画,20%文字
四、改善提案:
要求:简单,一页文件,目视化,可以手工写完。
五、改善新闻报:
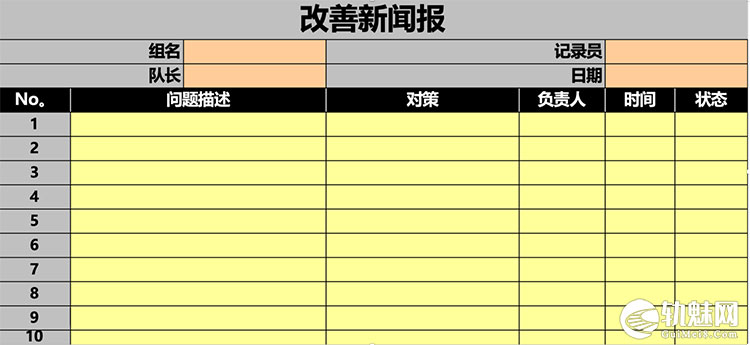
问题如何写:
- 基于事实,客观描述问题
- 识别问题会造成七大浪费中哪类浪费
- 总是关注流程问题,而不是个人
- 问五个为什么识别问题的根因
- 将大问题分解成若干小问题
对策如何写:
- 寻找那些你马上就可以尝试的方案
- 寻找那些不需要花钱的方案
- 寻找那些你能施加影响的方案
- 牢记要解决根因
- 可能会有多个行动项
- QC层别法:
口诀:层别分类别,查检收数据,柏拉抓重点,鱼骨找原因,散布看相关,直方显分布,管制做预防。
定义:按照原料、机器或操作人员等分别收集数据以找出期间差异并加以改善的方法。因不同需求目的而进行分类成不同的「类别」。从各类别中选取数据,分类,并进行分析的方法是容易观察,有效掌握事实的最有效、最简单的方法。
作用:1、发现问题,界定问题;2、发掘问题的要因;3、验证要因产生的影响。
项目与对象:

案例:用层别法分出安全问题发生因素。
七、QC查检表:
定义:以简单的数据、用容易了解的方式做成图形或表格。表中记有查检的必要项目,只要记上检查记号,并加以统计整理,就可做为进一步分析或核对检查之用。
作用:掌握问题点;掌握重要要因;确认改善效果。
应用场景:
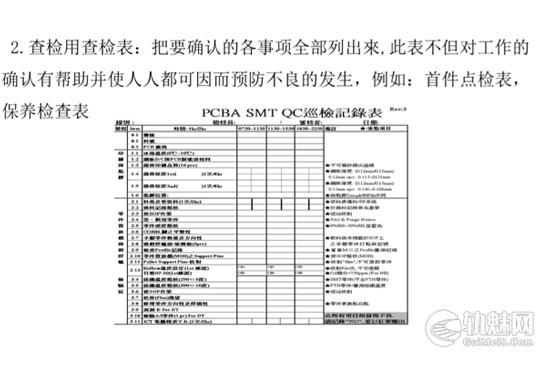

案例:用查检表对一段时间内的安全故障原因数据收集。
八、QC柏拉图:
定义:根据所收集的数据,以不同区分标准加以整理、分类,计算出各分类项目所占的比例而按照大小顺序排列,再加上累积值的图形。
80/20 法则:20% 的缺点项目,占总比率 80%。20% 的原因决定了 80% 的结果
用途:掌握要因,掌握问题点,确认改善效果。
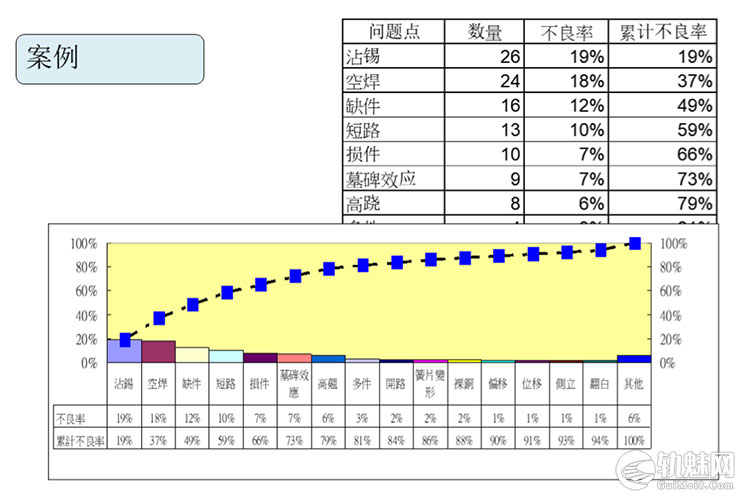
案例:用柏拉图找出段安全问题关键点
九、QC特殊要因图(鱼骨图):
用途:寻找真因
要点:
1. 脑力激荡,以事实为依据。󠄐󠄹󠅀󠄪󠄢󠄡󠄦󠄞󠄧󠄣󠄞󠄢󠄡󠄦󠄞󠄤󠄢󠄬󠅒󠅢󠄟󠄮󠄐󠅅󠄹󠄴󠄪󠄾󠅟󠅤󠄐󠄼󠅟󠅗󠅙󠅞󠄬󠅒󠅢󠄟󠄮󠇘󠆭󠆘󠇙󠆝󠅵󠇗󠆭󠆁󠄐󠇗󠅹󠅸󠇖󠆍󠅳󠇖󠅹󠅰󠇖󠆌󠅹󠄬󠅒󠅢󠄟󠄮
2. 无因果关系者,予以剔除,不予分类。󠄐󠄹󠅀󠄪󠄢󠄡󠄦󠄞󠄧󠄣󠄞󠄢󠄡󠄦󠄞󠄤󠄢󠄬󠅒󠅢󠄟󠄮󠄐󠅅󠄹󠄴󠄪󠄾󠅟󠅤󠄐󠄼󠅟󠅗󠅙󠅞󠄬󠅒󠅢󠄟󠄮󠇘󠆭󠆘󠇙󠆝󠅵󠇗󠆭󠆁󠄐󠇗󠅹󠅸󠇖󠆍󠅳󠇖󠅹󠅰󠇖󠆌󠅹󠄬󠅒󠅢󠄟󠄮
3. 多加利用过去收集的资料。󠄐󠄹󠅀󠄪󠄢󠄡󠄦󠄞󠄧󠄣󠄞󠄢󠄡󠄦󠄞󠄤󠄢󠄬󠅒󠅢󠄟󠄮󠄐󠅅󠄹󠄴󠄪󠄾󠅟󠅤󠄐󠄼󠅟󠅗󠅙󠅞󠄬󠅒󠅢󠄟󠄮󠇘󠆭󠆘󠇙󠆝󠅵󠇗󠆭󠆁󠄐󠇗󠅹󠅸󠇖󠆍󠅳󠇖󠅹󠅰󠇖󠆌󠅹󠄬󠅒󠅢󠄟󠄮
4. 依据特性别,分别制作不同的特性要因图。󠄐󠄹󠅀󠄪󠄢󠄡󠄦󠄞󠄧󠄣󠄞󠄢󠄡󠄦󠄞󠄤󠄢󠄬󠅒󠅢󠄟󠄮󠄐󠅅󠄹󠄴󠄪󠄾󠅟󠅤󠄐󠄼󠅟󠅗󠅙󠅞󠄬󠅒󠅢󠄟󠄮󠇘󠆭󠆘󠇙󠆝󠅵󠇗󠆭󠆁󠄐󠇗󠅹󠅸󠇖󠆍󠅳󠇖󠅹󠅰󠇖󠆌󠅹󠄬󠅒󠅢󠄟󠄮
5. 大要因通常代表是一个具体方向;中要因通常代表的是一个概念、想法;小要因通常代表的是具体事件。󠄐󠄹󠅀󠄪󠄢󠄡󠄦󠄞󠄧󠄣󠄞󠄢󠄡󠄦󠄞󠄤󠄢󠄬󠅒󠅢󠄟󠄮󠄐󠅅󠄹󠄴󠄪󠄾󠅟󠅤󠄐󠄼󠅟󠅗󠅙󠅞󠄬󠅒󠅢󠄟󠄮󠇘󠆭󠆘󠇙󠆝󠅵󠇗󠆭󠆁󠄐󠇗󠅹󠅸󠇖󠆍󠅳󠇖󠅹󠅰󠇖󠆌󠅹󠄬󠅒󠅢󠄟󠄮
6. 至少要有4根大骨、3根中骨及2根小骨,且这些要因都不能重复。󠄐󠄹󠅀󠄪󠄢󠄡󠄦󠄞󠄧󠄣󠄞󠄢󠄡󠄦󠄞󠄤󠄢󠄬󠅒󠅢󠄟󠄮󠄐󠅅󠄹󠄴󠄪󠄾󠅟󠅤󠄐󠄼󠅟󠅗󠅙󠅞󠄬󠅒󠅢󠄟󠄮󠇘󠆭󠆘󠇙󠆝󠅵󠇗󠆭󠆁󠄐󠇗󠅹󠅸󠇖󠆍󠅳󠇖󠅹󠅰󠇖󠆌󠅹󠄬󠅒󠅢󠄟󠄮
7. 重点放在解决问题上,并依结果提出对策,依5W2H原则执行。󠄐󠄹󠅀󠄪󠄢󠄡󠄦󠄞󠄧󠄣󠄞󠄢󠄡󠄦󠄞󠄤󠄢󠄬󠅒󠅢󠄟󠄮󠄐󠅅󠄹󠄴󠄪󠄾󠅟󠅤󠄐󠄼󠅟󠅗󠅙󠅞󠄬󠅒󠅢󠄟󠄮󠇘󠆭󠆘󠇙󠆝󠅵󠇗󠆭󠆁󠄐󠇗󠅹󠅸󠇖󠆍󠅳󠇖󠅹󠅰󠇖󠆌󠅹󠄬󠅒󠅢󠄟󠄮

十、QC散布图:
定义:把互相有关联的对应数据,在方格纸上以纵轴表示结果,以横轴表示原因;然后用点表示出分布形态,根据分布的形态来判断对应数据之间的相互关系。
· 相关分析:1、正相关 === 当一个变量增加,另一变量产生同样的增加趋势,则两个变量的关系是正相关;2、负相关 === 当一个变量增加,另一变量产生相反的降低趋势,则两个变量的关系是负相关;3、无相关 === 当两个变量之间不具备上述两种特征时,代表两者无相关。
用途:1、检定两变量间的相关性;2、从特性要求寻找最适要因;3、从要因预估特性水准。
应用场景:
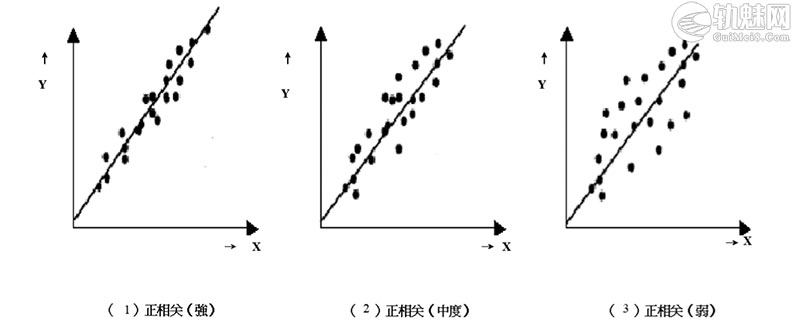
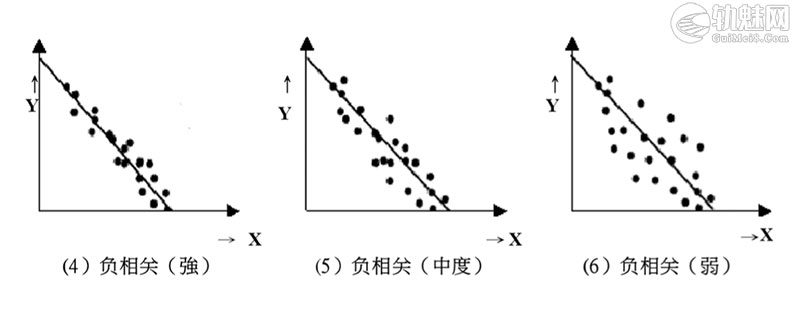

案例:用散点图确认安全措施与安全问题的相关性
十一、QC直方图:
定义:将所收集的数据、特性值或结果值,在横轴上适当地区分成几个相等区间,并将各区间内测定值所出现的次数累加起来,用柱形画出的图形。
步骤:
· 1、收集数据并且记录在纸上。󠄐󠄹󠅀󠄪󠄢󠄡󠄦󠄞󠄧󠄣󠄞󠄢󠄡󠄦󠄞󠄤󠄢󠄬󠅒󠅢󠄟󠄮󠄐󠅅󠄹󠄴󠄪󠄾󠅟󠅤󠄐󠄼󠅟󠅗󠅙󠅞󠄬󠅒󠅢󠄟󠄮󠇘󠆭󠆘󠇙󠆝󠅵󠇗󠆭󠆁󠄐󠇗󠅹󠅸󠇖󠆍󠅳󠇖󠅹󠅰󠇖󠆌󠅹󠄬󠅒󠅢󠄟󠄮
· 2、找出全体数据中之最大值(L)与最小值(S)。󠄐󠄹󠅀󠄪󠄢󠄡󠄦󠄞󠄧󠄣󠄞󠄢󠄡󠄦󠄞󠄤󠄢󠄬󠅒󠅢󠄟󠄮󠄐󠅅󠄹󠄴󠄪󠄾󠅟󠅤󠄐󠄼󠅟󠅗󠅙󠅞󠄬󠅒󠅢󠄟󠄮󠇘󠆭󠆘󠇙󠆝󠅵󠇗󠆭󠆁󠄐󠇗󠅹󠅸󠇖󠆍󠅳󠇖󠅹󠅰󠇖󠆌󠅹󠄬󠅒󠅢󠄟󠄮
· 3、定全距(R)= 最大值(L)- 最小值(S)。󠄐󠄹󠅀󠄪󠄢󠄡󠄦󠄞󠄧󠄣󠄞󠄢󠄡󠄦󠄞󠄤󠄢󠄬󠅒󠅢󠄟󠄮󠄐󠅅󠄹󠄴󠄪󠄾󠅟󠅤󠄐󠄼󠅟󠅗󠅙󠅞󠄬󠅒󠅢󠄟󠄮󠇘󠆭󠆘󠇙󠆝󠅵󠇗󠆭󠆁󠄐󠇗󠅹󠅸󠇖󠆍󠅳󠇖󠅹󠅰󠇖󠆌󠅹󠄬󠅒󠅢󠄟󠄮
· 4、决定组数󠄐󠄹󠅀󠄪󠄢󠄡󠄦󠄞󠄧󠄣󠄞󠄢󠄡󠄦󠄞󠄤󠄢󠄬󠅒󠅢󠄟󠄮󠄐󠅅󠄹󠄴󠄪󠄾󠅟󠅤󠄐󠄼󠅟󠅗󠅙󠅞󠄬󠅒󠅢󠄟󠄮󠇘󠆭󠆘󠇙󠆝󠅵󠇗󠆭󠆁󠄐󠇗󠅹󠅸󠇖󠆍󠅳󠇖󠅹󠅰󠇖󠆌󠅹󠄬󠅒󠅢󠄟󠄮
- 史特吉斯公式组数:K = 1 + 3.32log n(n = 数据个数)
- 组数决定参考表(经验法则):
- 数据数目 50 – 100,组数 6 – 10
- 数据数目 100 – 250,组数 7 – 12
- 数据数目 250 以上,组数 10 – 20
· 5、定组距(H)= R / K = 全距 / 组数
· 6、求各组上、下组界󠄐󠄹󠅀󠄪󠄢󠄡󠄦󠄞󠄧󠄣󠄞󠄢󠄡󠄦󠄞󠄤󠄢󠄬󠅒󠅢󠄟󠄮󠄐󠅅󠄹󠄴󠄪󠄾󠅟󠅤󠄐󠄼󠅟󠅗󠅙󠅞󠄬󠅒󠅢󠄟󠄮󠇘󠆭󠆘󠇙󠆝󠅵󠇗󠆭󠆁󠄐󠇗󠅹󠅸󠇖󠆍󠅳󠇖󠅹󠅰󠇖󠆌󠅹󠄬󠅒󠅢󠄟󠄮
- 第一组下组界 = 最小值 – 最小测定值 / 2
- 第一组上组界 = 下组界 + 组距(以此类推)
· 7、决定组的中心点。(上组界 + 下组界)/ 2 = 组的中心点
· 8、制作次数分配表。󠄐󠄹󠅀󠄪󠄢󠄡󠄦󠄞󠄧󠄣󠄞󠄢󠄡󠄦󠄞󠄤󠄢󠄬󠅒󠅢󠄟󠄮󠄐󠅅󠄹󠄴󠄪󠄾󠅟󠅤󠄐󠄼󠅟󠅗󠅙󠅞󠄬󠅒󠅢󠄟󠄮󠇘󠆭󠆘󠇙󠆝󠅵󠇗󠆭󠆁󠄐󠇗󠅹󠅸󠇖󠆍󠅳󠇖󠅹󠅰󠇖󠆌󠅹󠄬󠅒󠅢󠄟󠄮
· 9、制作直方图。󠄐󠄹󠅀󠄪󠄢󠄡󠄦󠄞󠄧󠄣󠄞󠄢󠄡󠄦󠄞󠄤󠄢󠄬󠅒󠅢󠄟󠄮󠄐󠅅󠄹󠄴󠄪󠄾󠅟󠅤󠄐󠄼󠅟󠅗󠅙󠅞󠄬󠅒󠅢󠄟󠄮󠇘󠆭󠆘󠇙󠆝󠅵󠇗󠆭󠆁󠄐󠇗󠅹󠅸󠇖󠆍󠅳󠇖󠅹󠅰󠇖󠆌󠅹󠄬󠅒󠅢󠄟󠄮
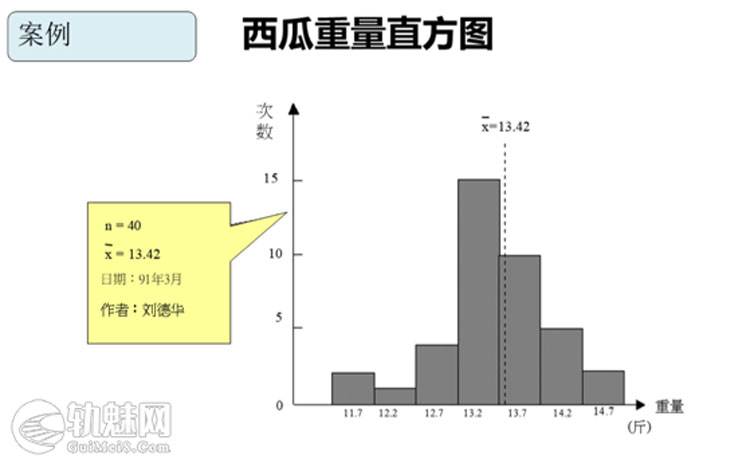
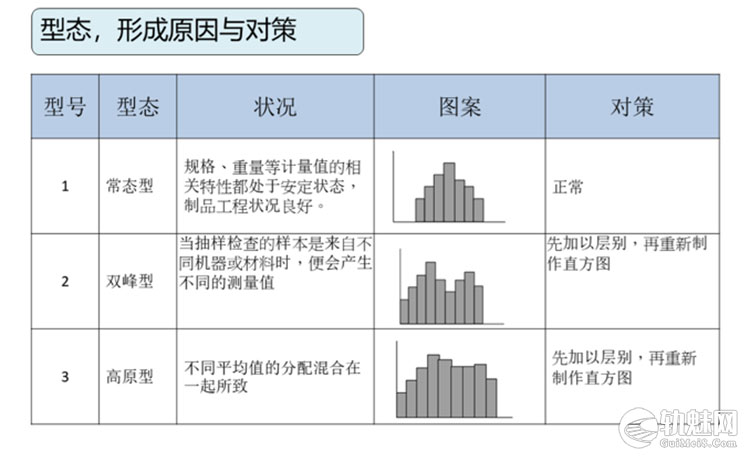

十二、QC管制图:
定义:将实际的品质特性,按时间的先后或制品全体号码的次序,与根据过去检验所建立的制程能力的管制界限比较,以判断产品品质是否安定的一种图形。
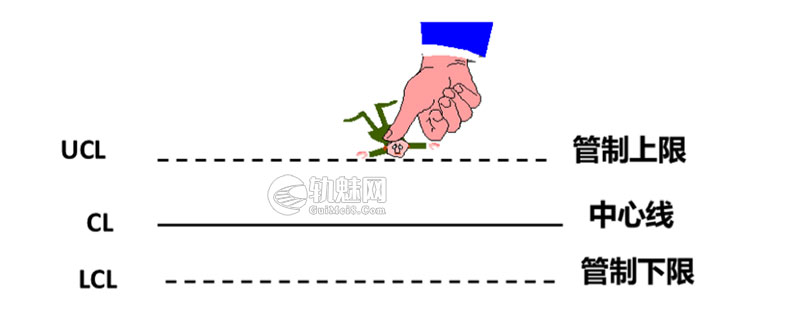
目的:防止偶然原因再次发生,维持过程稳定。
分类:
依数据的性质分类
- 计量管制图
- 用来测量长度、重量、面积、时间等计量值的管制图。
- 计数值管制图
- 用来计算不良数、缺点数等计数值的管制图。
依用途来分类
- 解析用管制图
- 为了调查制程是否处于统计管制的状态。
- 管制用管制图
- 为了保持完善管理的制程。
案例:用管制图制定作业标准。
第二部分:质量改善
十三、A3报告:
- 步骤:课题背景→现状和目标→原因分析→改善计划→实施跟进→标准化和总结
- 适用:解决需深度分析、跨部门协作且影响任务目标的复杂问题。

十四、Why-Why分析:
定义:WHY WHY分析是将发现的现象使用系统化的思考模式由应有的状态或人机料法环的关系或原理原则筛选出引起现象的因素,再以筛选出的因素为基本,一面仔细观察调查现场现物,一面追求真正的原因并且研究再发防止对策。
WHY WHY分析是将发现的现象连续进行多次思考“为什么”的动作,直到问到最终的原因,并依据实际值和标准值的比对,判定要因是否成立,然后对真因作有效对策的方法.󠄐󠄹󠅀󠄪󠄢󠄡󠄦󠄞󠄧󠄣󠄞󠄢󠄡󠄦󠄞󠄤󠄢󠄬󠅒󠅢󠄟󠄮󠄐󠅅󠄹󠄴󠄪󠄾󠅟󠅤󠄐󠄼󠅟󠅗󠅙󠅞󠄬󠅒󠅢󠄟󠄮󠇘󠆭󠆘󠇙󠆝󠅵󠇗󠆭󠆁󠄐󠇗󠅹󠅸󠇖󠆍󠅳󠇖󠅹󠅰󠇖󠆌󠅹󠄬󠅒󠅢󠄟󠄮
- 适用:适用于现象比较容易明确,原因接近于单独原因的情况。
- 要点:确保why到最后;避免不自然的推论(借口类);避免牵涉人的心理;避免责任推卸;层与层间逻辑性;对分析结果的确认。
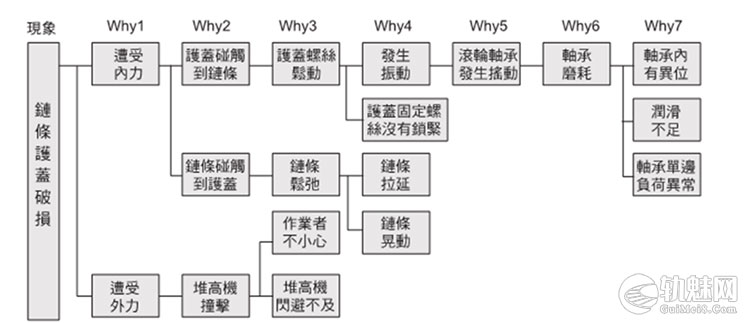
十五、FTA故障树分析
1.定义:FTA基本概念
顶事件(Top Event):分析的最终目标事件(如”电梯困人”);󠄐󠄹󠅀󠄪󠄢󠄡󠄦󠄞󠄧󠄣󠄞󠄢󠄡󠄦󠄞󠄤󠄢󠄬󠅒󠅢󠄟󠄮󠄐󠅅󠄹󠄴󠄪󠄾󠅟󠅤󠄐󠄼󠅟󠅗󠅙󠅞󠄬󠅒󠅢󠄟󠄮󠇘󠆭󠆘󠇙󠆝󠅵󠇗󠆭󠆁󠄐󠇗󠅹󠅸󠇖󠆍󠅳󠇖󠅹󠅰󠇖󠆌󠅹󠄬󠅒󠅢󠄟󠄮
中间事件(Intermediate Event):由其他事件组合导致的事件;󠄐󠄹󠅀󠄪󠄢󠄡󠄦󠄞󠄧󠄣󠄞󠄢󠄡󠄦󠄞󠄤󠄢󠄬󠅒󠅢󠄟󠄮󠄐󠅅󠄹󠄴󠄪󠄾󠅟󠅤󠄐󠄼󠅟󠅗󠅙󠅞󠄬󠅒󠅢󠄟󠄮󠇘󠆭󠆘󠇙󠆝󠅵󠇗󠆭󠆁󠄐󠇗󠅹󠅸󠇖󠆍󠅳󠇖󠅹󠅰󠇖󠆌󠅹󠄬󠅒󠅢󠄟󠄮
底事件(Basic Event):无法进一步分解的基本故障或原因(如”电池老化”)。󠄐󠄹󠅀󠄪󠄢󠄡󠄦󠄞󠄧󠄣󠄞󠄢󠄡󠄦󠄞󠄤󠄢󠄬󠅒󠅢󠄟󠄮󠄐󠅅󠄹󠄴󠄪󠄾󠅟󠅤󠄐󠄼󠅟󠅗󠅙󠅞󠄬󠅒󠅢󠄟󠄮󠇘󠆭󠆘󠇙󠆝󠅵󠇗󠆭󠆁󠄐󠇗󠅹󠅸󠇖󠆍󠅳󠇖󠅹󠅰󠇖󠆌󠅹󠄬󠅒󠅢󠄟󠄮
逻辑门:与门(AND Gate):所有输入事件同时发生,才能导致输出事件;或门(OR Gate):任一输入事件发生即导致输出事件;其他门(如非门、表决门等)用于特定场景。󠄐󠄹󠅀󠄪󠄢󠄡󠄦󠄞󠄧󠄣󠄞󠄢󠄡󠄦󠄞󠄤󠄢󠄬󠅒󠅢󠄟󠄮󠄐󠅅󠄹󠄴󠄪󠄾󠅟󠅤󠄐󠄼󠅟󠅗󠅙󠅞󠄬󠅒󠅢󠄟󠄮󠇘󠆭󠆘󠇙󠆝󠅵󠇗󠆭󠆁󠄐󠇗󠅹󠅸󠇖󠆍󠅳󠇖󠅹󠅰󠇖󠆌󠅹󠄬󠅒󠅢󠄟󠄮
2.实施步骤
定义顶事件:明确分析目标(如”汽车无法启动”)。󠄐󠄹󠅀󠄪󠄢󠄡󠄦󠄞󠄧󠄣󠄞󠄢󠄡󠄦󠄞󠄤󠄢󠄬󠅒󠅢󠄟󠄮󠄐󠅅󠄹󠄴󠄪󠄾󠅟󠅤󠄐󠄼󠅟󠅗󠅙󠅞󠄬󠅒󠅢󠄟󠄮󠇘󠆭󠆘󠇙󠆝󠅵󠇗󠆭󠆁󠄐󠇗󠅹󠅸󠇖󠆍󠅳󠇖󠅹󠅰󠇖󠆌󠅹󠄬󠅒󠅢󠄟󠄮
构建故障树:自顶向下分解,使用逻辑门连接事件。󠄐󠄹󠅀󠄪󠄢󠄡󠄦󠄞󠄧󠄣󠄞󠄢󠄡󠄦󠄞󠄤󠄢󠄬󠅒󠅢󠄟󠄮󠄐󠅅󠄹󠄴󠄪󠄾󠅟󠅤󠄐󠄼󠅟󠅗󠅙󠅞󠄬󠅒󠅢󠄟󠄮󠇘󠆭󠆘󠇙󠆝󠅵󠇗󠆭󠆁󠄐󠇗󠅹󠅸󠇖󠆍󠅳󠇖󠅹󠅰󠇖󠆌󠅹󠄬󠅒󠅢󠄟󠄮
分解至底事件(如”燃油泵故障”)󠄐󠄹󠅀󠄪󠄢󠄡󠄦󠄞󠄧󠄣󠄞󠄢󠄡󠄦󠄞󠄤󠄢󠄬󠅒󠅢󠄟󠄮󠄐󠅅󠄹󠄴󠄪󠄾󠅟󠅤󠄐󠄼󠅟󠅗󠅙󠅞󠄬󠅒󠅢󠄟󠄮󠇘󠆭󠆘󠇙󠆝󠅵󠇗󠆭󠆁󠄐󠇗󠅹󠅸󠇖󠆍󠅳󠇖󠅹󠅰󠇖󠆌󠅹󠄬󠅒󠅢󠄟󠄮
十六、质量改善周模式
1.作用:从做中学习、培养人才;改善流程、提升绩效;团队协作、组织成长;全员参与、范式转变。

2.改善周常见问题:
为什么要5天?
答:精益是高级运营管理模式/方法多数是反常识的,需要反复的培训及实践来领会吸收。
现场突破的需要 – 制作新工具/设备,制定新的流程/标准,整理现场,人员培训均需要时间。
为什么要跨部门团队?
答:便于了解上下游流程的运作及其影响;便于快速实施改善创意;便于进行流程优化,创造新标准。
3.改善周立项书:
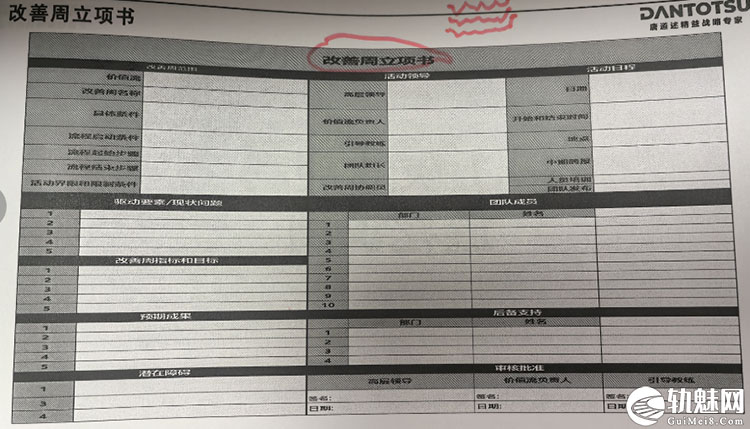
4.改善周和精益改善项目:

十七、流程地图



十八、流程指标树
定义:指标树的”树根”(即分解起点)通常是企业经营..业绩的根本性指标和经营业绩的最终体现;一个指标树可有多种分解方式,选择何种分解方式应以最有利于分析企业业务构成,深度挖掘企业经营潜力为标准;指标树的分解必须层层细化,分解得越细可操作性越强。注:一般组成9层。
示例:
十九、质量控制VOC-CTQ
1.定义:VOC客户之声
2、VOC三个要素:客户之声指的是你从市场收集信息的所有方式;使用客户信息的声音可以提高对当前或未来产品和服务的认识、机会或问题的认识;客户之声提供数据,以集中设计和实施满足/超过用户期望的解决方案。󠄐󠄹󠅀󠄪󠄢󠄡󠄦󠄞󠄧󠄣󠄞󠄢󠄡󠄦󠄞󠄤󠄢󠄬󠅒󠅢󠄟󠄮󠄐󠅅󠄹󠄴󠄪󠄾󠅟󠅤󠄐󠄼󠅟󠅗󠅙󠅞󠄬󠅒󠅢󠄟󠄮󠇘󠆭󠆘󠇙󠆝󠅵󠇗󠆭󠆁󠄐󠇗󠅹󠅸󠇖󠆍󠅳󠇖󠅹󠅰󠇖󠆌󠅹󠄬󠅒󠅢󠄟󠄮
3、VOC方法应用程序:识别客户,决定需要了解的内容→制定收集计划,收集客户反馈数据→分析数据,用客户的语言列出需求表→给CTQs设定规格→将客户需求转换成CTQs→将客户需求进行分类。󠄐󠄹󠅀󠄪󠄢󠄡󠄦󠄞󠄧󠄣󠄞󠄢󠄡󠄦󠄞󠄤󠄢󠄬󠅒󠅢󠄟󠄮󠄐󠅅󠄹󠄴󠄪󠄾󠅟󠅤󠄐󠄼󠅟󠅗󠅙󠅞󠄬󠅒󠅢󠄟󠄮󠇘󠆭󠆘󠇙󠆝󠅵󠇗󠆭󠆁󠄐󠇗󠅹󠅸󠇖󠆍󠅳󠇖󠅹󠅰󠇖󠆌󠅹󠄬󠅒󠅢󠄟󠄮

二十、质量控制VOC-CTQ
1、定义:VOC客户之声
2、VOC三个要素:客户之声指的是你从市场收集信息的所有方式;使用客户信息的声音可以提高对当前或未来产品和服务的认识、机会或问题的认识;客户之声提供数据,以集中设计和实施满足/超过用户期望的解决方案。󠄐󠄹󠅀󠄪󠄢󠄡󠄦󠄞󠄧󠄣󠄞󠄢󠄡󠄦󠄞󠄤󠄢󠄬󠅒󠅢󠄟󠄮󠄐󠅅󠄹󠄴󠄪󠄾󠅟󠅤󠄐󠄼󠅟󠅗󠅙󠅞󠄬󠅒󠅢󠄟󠄮󠇘󠆭󠆘󠇙󠆝󠅵󠇗󠆭󠆁󠄐󠇗󠅹󠅸󠇖󠆍󠅳󠇖󠅹󠅰󠇖󠆌󠅹󠄬󠅒󠅢󠄟󠄮
3、VOC方法应用程序:识别客户,决定需要了解的内容→制定收集计划,收集客户反馈数据→分析数据,用客户的语言列出需求表→给CTQs设定规格→将客户需求转换成CTQs→将客户需求进行分类。󠄐󠄹󠅀󠄪󠄢󠄡󠄦󠄞󠄧󠄣󠄞󠄢󠄡󠄦󠄞󠄤󠄢󠄬󠅒󠅢󠄟󠄮󠄐󠅅󠄹󠄴󠄪󠄾󠅟󠅤󠄐󠄼󠅟󠅗󠅙󠅞󠄬󠅒󠅢󠄟󠄮󠇘󠆭󠆘󠇙󠆝󠅵󠇗󠆭󠆁󠄐󠇗󠅹󠅸󠇖󠆍󠅳󠇖󠅹󠅰󠇖󠆌󠅹󠄬󠅒󠅢󠄟󠄮

第三部分:质量控制
二十一、卡诺模型
概念:

案例:

二十二、目视化管理看板
概念:

1.目视化管理可以帮助我们:
①展示和对比数据;②识别差异;③识别问题;④设备状态;⑤结构和关系。󠄐󠄹󠅀󠄪󠄢󠄡󠄦󠄞󠄧󠄣󠄞󠄢󠄡󠄦󠄞󠄤󠄢󠄬󠅒󠅢󠄟󠄮󠄐󠅅󠄹󠄴󠄪󠄾󠅟󠅤󠄐󠄼󠅟󠅗󠅙󠅞󠄬󠅒󠅢󠄟󠄮󠇘󠆭󠆘󠇙󠆝󠅵󠇗󠆭󠆁󠄐󠇗󠅹󠅸󠇖󠆍󠅳󠇖󠅹󠅰󠇖󠆌󠅹󠄬󠅒󠅢󠄟󠄮
2.目视管理沟通版的作用
①允许个人发挥应用自己的知识,经验和创造性;发表各自的意见;共同参与决策;了解对自己和客户来说什么是重要的,这样有助于更好的完成工作。②促进团队合作及分享主人翁精神③信息公开,让每个人知晓④提倡和表彰团队价值的作用⑤跨部门学习和信息共享󠄐󠄹󠅀󠄪󠄢󠄡󠄦󠄞󠄧󠄣󠄞󠄢󠄡󠄦󠄞󠄤󠄢󠄬󠅒󠅢󠄟󠄮󠄐󠅅󠄹󠄴󠄪󠄾󠅟󠅤󠄐󠄼󠅟󠅗󠅙󠅞󠄬󠅒󠅢󠄟󠄮󠇘󠆭󠆘󠇙󠆝󠅵󠇗󠆭󠆁󠄐󠇗󠅹󠅸󠇖󠆍󠅳󠇖󠅹󠅰󠇖󠆌󠅹󠄬󠅒󠅢󠄟󠄮
3.目视化沟通板三个关注点:人员、绩效表现、持续改善󠄐󠄹󠅀󠄪󠄢󠄡󠄦󠄞󠄧󠄣󠄞󠄢󠄡󠄦󠄞󠄤󠄢󠄬󠅒󠅢󠄟󠄮󠄐󠅅󠄹󠄴󠄪󠄾󠅟󠅤󠄐󠄼󠅟󠅗󠅙󠅞󠄬󠅒󠅢󠄟󠄮󠇘󠆭󠆘󠇙󠆝󠅵󠇗󠆭󠆁󠄐󠇗󠅹󠅸󠇖󠆍󠅳󠇖󠅹󠅰󠇖󠆌󠅹󠄬󠅒󠅢󠄟󠄮
案例:
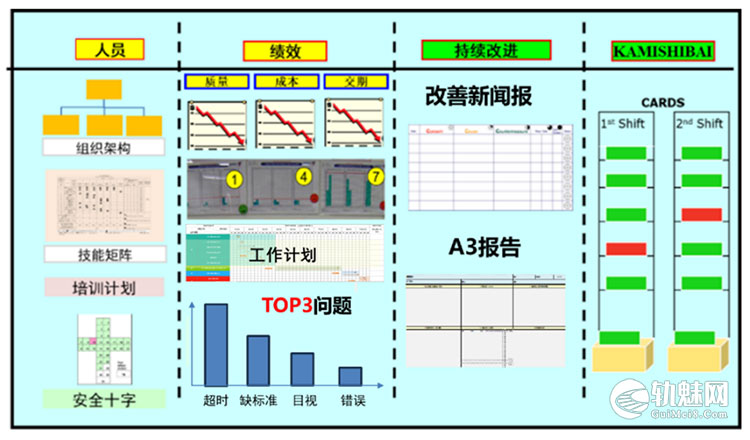

二十三、快反系统
概念:帮助链是当出现生产、质量、物流、维修和安全等方面的问题时,力争将损失降到最低,使之能够迅速恢复到正常流程的一种快速反应体系。包含:安灯系统Andon、快速反应计划、人员可视化管理、帮助链可视化管理板、异常问题分析、帮助链每日例会、标准化。
案例:


人员可视化管理、帮助连可视化管理板、异常问题分析、帮助链每日例会、标准化.
二十四、变化点管理
概念:质量问题的实质(对现状的认识)。
质量问题是由一些变化点引起的󠄐󠄹󠅀󠄪󠄢󠄡󠄦󠄞󠄧󠄣󠄞󠄢󠄡󠄦󠄞󠄤󠄢󠄬󠅒󠅢󠄟󠄮󠄐󠅅󠄹󠄴󠄪󠄾󠅟󠅤󠄐󠄼󠅟󠅗󠅙󠅞󠄬󠅒󠅢󠄟󠄮󠇘󠆭󠆘󠇙󠆝󠅵󠇗󠆭󠆁󠄐󠇗󠅹󠅸󠇖󠆍󠅳󠇖󠅹󠅰󠇖󠆌󠅹󠄬󠅒󠅢󠄟󠄮
·【变化点】发生时,未能遵守相应规定(培训·监督不足)󠄐󠄹󠅀󠄪󠄢󠄡󠄦󠄞󠄧󠄣󠄞󠄢󠄡󠄦󠄞󠄤󠄢󠄬󠅒󠅢󠄟󠄮󠄐󠅅󠄹󠄴󠄪󠄾󠅟󠅤󠄐󠄼󠅟󠅗󠅙󠅞󠄬󠅒󠅢󠄟󠄮󠇘󠆭󠆘󠇙󠆝󠅵󠇗󠆭󠆁󠄐󠇗󠅹󠅸󠇖󠆍󠅳󠇖󠅹󠅰󠇖󠆌󠅹󠄬󠅒󠅢󠄟󠄮
·【变化点】发生时,相应规定不明确(标准书不完善)󠄐󠄹󠅀󠄪󠄢󠄡󠄦󠄞󠄧󠄣󠄞󠄢󠄡󠄦󠄞󠄤󠄢󠄬󠅒󠅢󠄟󠄮󠄐󠅅󠄹󠄴󠄪󠄾󠅟󠅤󠄐󠄼󠅟󠅗󠅙󠅞󠄬󠅒󠅢󠄟󠄮󠇘󠆭󠆘󠇙󠆝󠅵󠇗󠆭󠆁󠄐󠇗󠅹󠅸󠇖󠆍󠅳󠇖󠅹󠅰󠇖󠆌󠅹󠄬󠅒󠅢󠄟󠄮
·【变化点】发生时,没有意识到是变化点(意识的欠缺)󠄐󠄹󠅀󠄪󠄢󠄡󠄦󠄞󠄧󠄣󠄞󠄢󠄡󠄦󠄞󠄤󠄢󠄬󠅒󠅢󠄟󠄮󠄐󠅅󠄹󠄴󠄪󠄾󠅟󠅤󠄐󠄼󠅟󠅗󠅙󠅞󠄬󠅒󠅢󠄟󠄮󠇘󠆭󠆘󠇙󠆝󠅵󠇗󠆭󠆁󠄐󠇗󠅹󠅸󠇖󠆍󠅳󠇖󠅹󠅰󠇖󠆌󠅹󠄬󠅒󠅢󠄟󠄮
由于以上原因导致的质量问题并不少见。󠄐󠄹󠅀󠄪󠄢󠄡󠄦󠄞󠄧󠄣󠄞󠄢󠄡󠄦󠄞󠄤󠄢󠄬󠅒󠅢󠄟󠄮󠄐󠅅󠄹󠄴󠄪󠄾󠅟󠅤󠄐󠄼󠅟󠅗󠅙󠅞󠄬󠅒󠅢󠄟󠄮󠇘󠆭󠆘󠇙󠆝󠅵󠇗󠆭󠆁󠄐󠇗󠅹󠅸󠇖󠆍󠅳󠇖󠅹󠅰󠇖󠆌󠅹󠄬󠅒󠅢󠄟󠄮
另外在日常的工作当中,变化点。󠄐󠄹󠅀󠄪󠄢󠄡󠄦󠄞󠄧󠄣󠄞󠄢󠄡󠄦󠄞󠄤󠄢󠄬󠅒󠅢󠄟󠄮󠄐󠅅󠄹󠄴󠄪󠄾󠅟󠅤󠄐󠄼󠅟󠅗󠅙󠅞󠄬󠅒󠅢󠄟󠄮󠇘󠆭󠆘󠇙󠆝󠅵󠇗󠆭󠆁󠄐󠇗󠅹󠅸󠇖󠆍󠅳󠇖󠅹󠅰󠇖󠆌󠅹󠄬󠅒󠅢󠄟󠄮
总之,为使因变化点而导致的质量问题(风险)能够被①尽早察觉(预知危险,尽早发现危险)②防患未然(未然防止)③杜绝流出(流出防止)󠄐󠄹󠅀󠄪󠄢󠄡󠄦󠄞󠄧󠄣󠄞󠄢󠄡󠄦󠄞󠄤󠄢󠄬󠅒󠅢󠄟󠄮󠄐󠅅󠄹󠄴󠄪󠄾󠅟󠅤󠄐󠄼󠅟󠅗󠅙󠅞󠄬󠅒󠅢󠄟󠄮󠇘󠆭󠆘󠇙󠆝󠅵󠇗󠆭󠆁󠄐󠇗󠅹󠅸󠇖󠆍󠅳󠇖󠅹󠅰󠇖󠆌󠅹󠄬󠅒󠅢󠄟󠄮
需要建立并维持可以察觉到变化点并能处理的体制→变化点管理󠄐󠄹󠅀󠄪󠄢󠄡󠄦󠄞󠄧󠄣󠄞󠄢󠄡󠄦󠄞󠄤󠄢󠄬󠅒󠅢󠄟󠄮󠄐󠅅󠄹󠄴󠄪󠄾󠅟󠅤󠄐󠄼󠅟󠅗󠅙󠅞󠄬󠅒󠅢󠄟󠄮󠇘󠆭󠆘󠇙󠆝󠅵󠇗󠆭󠆁󠄐󠇗󠅹󠅸󠇖󠆍󠅳󠇖󠅹󠅰󠇖󠆌󠅹󠄬󠅒󠅢󠄟󠄮

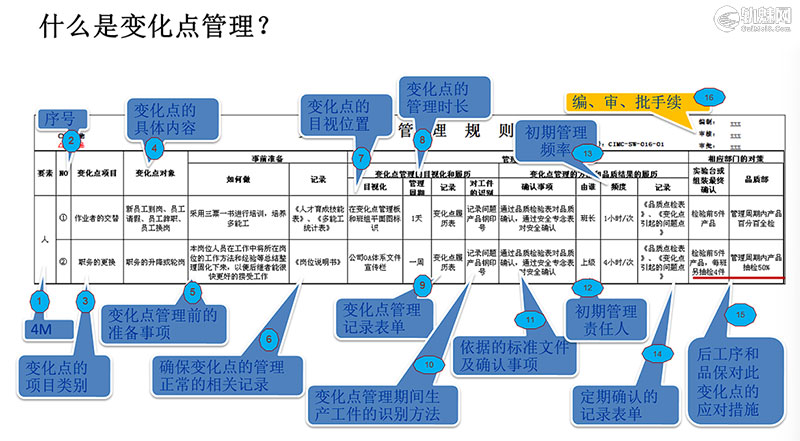
二十五、分层审核——纸卡系统
概念:在日语中意思为连环画剧,即使用纸卡一边是图画,另一边写着文字描述,用于幼儿教育;在工作现场用于检查回顾关键控制点或控制标准的一套卡片系统;是关于安全、品质、交货、成本、效率等标准的检验卡。
案例:
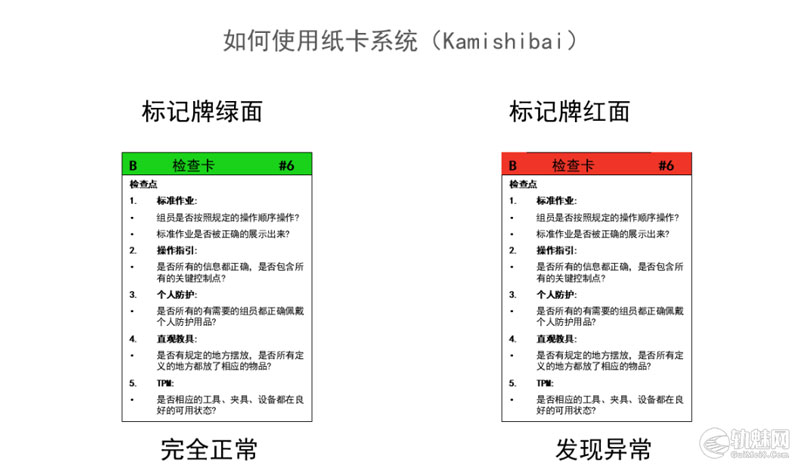

二十六、FEMA失效模式与效应分析
概念:
1.FMEA是一组系统化的活动,其目的是:󠄐󠄹󠅀󠄪󠄢󠄡󠄦󠄞󠄧󠄣󠄞󠄢󠄡󠄦󠄞󠄤󠄢󠄬󠅒󠅢󠄟󠄮󠄐󠅅󠄹󠄴󠄪󠄾󠅟󠅤󠄐󠄼󠅟󠅗󠅙󠅞󠄬󠅒󠅢󠄟󠄮󠇘󠆭󠆘󠇙󠆝󠅵󠇗󠆭󠆁󠄐󠇗󠅹󠅸󠇖󠆍󠅳󠇖󠅹󠅰󠇖󠆌󠅹󠄬󠅒󠅢󠄟󠄮
①发现、评价产品/过程中潜在的失效及其后果;󠄐󠄹󠅀󠄪󠄢󠄡󠄦󠄞󠄧󠄣󠄞󠄢󠄡󠄦󠄞󠄤󠄢󠄬󠅒󠅢󠄟󠄮󠄐󠅅󠄹󠄴󠄪󠄾󠅟󠅤󠄐󠄼󠅟󠅗󠅙󠅞󠄬󠅒󠅢󠄟󠄮󠇘󠆭󠆘󠇙󠆝󠅵󠇗󠆭󠆁󠄐󠇗󠅹󠅸󠇖󠆍󠅳󠇖󠅹󠅰󠇖󠆌󠅹󠄬󠅒󠅢󠄟󠄮
②找到能够避免或减少这些潜在失效发生的措施;󠄐󠄹󠅀󠄪󠄢󠄡󠄦󠄞󠄧󠄣󠄞󠄢󠄡󠄦󠄞󠄤󠄢󠄬󠅒󠅢󠄟󠄮󠄐󠅅󠄹󠄴󠄪󠄾󠅟󠅤󠄐󠄼󠅟󠅗󠅙󠅞󠄬󠅒󠅢󠄟󠄮󠇘󠆭󠆘󠇙󠆝󠅵󠇗󠆭󠆁󠄐󠇗󠅹󠅸󠇖󠆍󠅳󠇖󠅹󠅰󠇖󠆌󠅹󠄬󠅒󠅢󠄟󠄮
③书面总结上述过程。
2.他是对涉及(产品/过程)过程的完善,以明确什么样的设计才能满足顾客要求。󠄐󠄹󠅀󠄪󠄢󠄡󠄦󠄞󠄧󠄣󠄞󠄢󠄡󠄦󠄞󠄤󠄢󠄬󠅒󠅢󠄟󠄮󠄐󠅅󠄹󠄴󠄪󠄾󠅟󠅤󠄐󠄼󠅟󠅗󠅙󠅞󠄬󠅒󠅢󠄟󠄮󠇘󠆭󠆘󠇙󠆝󠅵󠇗󠆭󠆁󠄐󠇗󠅹󠅸󠇖󠆍󠅳󠇖󠅹󠅰󠇖󠆌󠅹󠄬󠅒󠅢󠄟󠄮
3.FMEA重点在于设计,无论是设计开发产品,还是过程设计。󠄐󠄹󠅀󠄪󠄢󠄡󠄦󠄞󠄧󠄣󠄞󠄢󠄡󠄦󠄞󠄤󠄢󠄬󠅒󠅢󠄟󠄮󠄐󠅅󠄹󠄴󠄪󠄾󠅟󠅤󠄐󠄼󠅟󠅗󠅙󠅞󠄬󠅒󠅢󠄟󠄮󠇘󠆭󠆘󠇙󠆝󠅵󠇗󠆭󠆁󠄐󠇗󠅹󠅸󠇖󠆍󠅳󠇖󠅹󠅰󠇖󠆌󠅹󠄬󠅒󠅢󠄟󠄮
4.严重度,发生率,难检度,风险优先数󠄐󠄹󠅀󠄪󠄢󠄡󠄦󠄞󠄧󠄣󠄞󠄢󠄡󠄦󠄞󠄤󠄢󠄬󠅒󠅢󠄟󠄮󠄐󠅅󠄹󠄴󠄪󠄾󠅟󠅤󠄐󠄼󠅟󠅗󠅙󠅞󠄬󠅒󠅢󠄟󠄮󠇘󠆭󠆘󠇙󠆝󠅵󠇗󠆭󠆁󠄐󠇗󠅹󠅸󠇖󠆍󠅳󠇖󠅹󠅰󠇖󠆌󠅹󠄬󠅒󠅢󠄟󠄮
严重度(1-10):S;发生率(1-10):O;难检度(1-10):D;风险优先数:RPN=S*O*D;󠄐󠄹󠅀󠄪󠄢󠄡󠄦󠄞󠄧󠄣󠄞󠄢󠄡󠄦󠄞󠄤󠄢󠄬󠅒󠅢󠄟󠄮󠄐󠅅󠄹󠄴󠄪󠄾󠅟󠅤󠄐󠄼󠅟󠅗󠅙󠅞󠄬󠅒󠅢󠄟󠄮󠇘󠆭󠆘󠇙󠆝󠅵󠇗󠆭󠆁󠄐󠇗󠅹󠅸󠇖󠆍󠅳󠇖󠅹󠅰󠇖󠆌󠅹󠄬󠅒󠅢󠄟󠄮
5.所有流程:过程-客户要求-特性描述-暴露问题(和“要有检测的方法和标准”相互作用)-评估后果。󠄐󠄹󠅀󠄪󠄢󠄡󠄦󠄞󠄧󠄣󠄞󠄢󠄡󠄦󠄞󠄤󠄢󠄬󠅒󠅢󠄟󠄮󠄐󠅅󠄹󠄴󠄪󠄾󠅟󠅤󠄐󠄼󠅟󠅗󠅙󠅞󠄬󠅒󠅢󠄟󠄮󠇘󠆭󠆘󠇙󠆝󠅵󠇗󠆭󠆁󠄐󠇗󠅹󠅸󠇖󠆍󠅳󠇖󠅹󠅰󠇖󠆌󠅹󠄬󠅒󠅢󠄟󠄮
P-FMEA:过程失效模式;D-FMEA:设计失效模式。󠄐󠄹󠅀󠄪󠄢󠄡󠄦󠄞󠄧󠄣󠄞󠄢󠄡󠄦󠄞󠄤󠄢󠄬󠅒󠅢󠄟󠄮󠄐󠅅󠄹󠄴󠄪󠄾󠅟󠅤󠄐󠄼󠅟󠅗󠅙󠅞󠄬󠅒󠅢󠄟󠄮󠇘󠆭󠆘󠇙󠆝󠅵󠇗󠆭󠆁󠄐󠇗󠅹󠅸󠇖󠆍󠅳󠇖󠅹󠅰󠇖󠆌󠅹󠄬󠅒󠅢󠄟󠄮
案例:

第四部分 质量设计
二十七、Control Plan控制计划
概念:该文件是当前使用的失效模式分析控制方法的扩充内容。
1.对于每一种关键质量特征和输入,都应该明确测量系统的能力(测量系统再现性和重复性 ) 。󠄐󠄹󠅀󠄪󠄢󠄡󠄦󠄞󠄧󠄣󠄞󠄢󠄡󠄦󠄞󠄤󠄢󠄬󠅒󠅢󠄟󠄮󠄐󠅅󠄹󠄴󠄪󠄾󠅟󠅤󠄐󠄼󠅟󠅗󠅙󠅞󠄬󠅒󠅢󠄟󠄮󠇘󠆭󠆘󠇙󠆝󠅵󠇗󠆭󠆁󠄐󠇗󠅹󠅸󠇖󠆍󠅳󠇖󠅹󠅰󠇖󠆌󠅹󠄬󠅒󠅢󠄟󠄮
2.对于变量数据,应该计算出Sigma值。󠄐󠄹󠅀󠄪󠄢󠄡󠄦󠄞󠄧󠄣󠄞󠄢󠄡󠄦󠄞󠄤󠄢󠄬󠅒󠅢󠄟󠄮󠄐󠅅󠄹󠄴󠄪󠄾󠅟󠅤󠄐󠄼󠅟󠅗󠅙󠅞󠄬󠅒󠅢󠄟󠄮󠇘󠆭󠆘󠇙󠆝󠅵󠇗󠆭󠆁󠄐󠇗󠅹󠅸󠇖󠆍󠅳󠇖󠅹󠅰󠇖󠆌󠅹󠄬󠅒󠅢󠄟󠄮
3.应该列出与有关响应计划对应的采样计划及其实施规定。󠄐󠄹󠅀󠄪󠄢󠄡󠄦󠄞󠄧󠄣󠄞󠄢󠄡󠄦󠄞󠄤󠄢󠄬󠅒󠅢󠄟󠄮󠄐󠅅󠄹󠄴󠄪󠄾󠅟󠅤󠄐󠄼󠅟󠅗󠅙󠅞󠄬󠅒󠅢󠄟󠄮󠇘󠆭󠆘󠇙󠆝󠅵󠇗󠆭󠆁󠄐󠇗󠅹󠅸󠇖󠆍󠅳󠇖󠅹󠅰󠇖󠆌󠅹󠄬󠅒󠅢󠄟󠄮
案例:
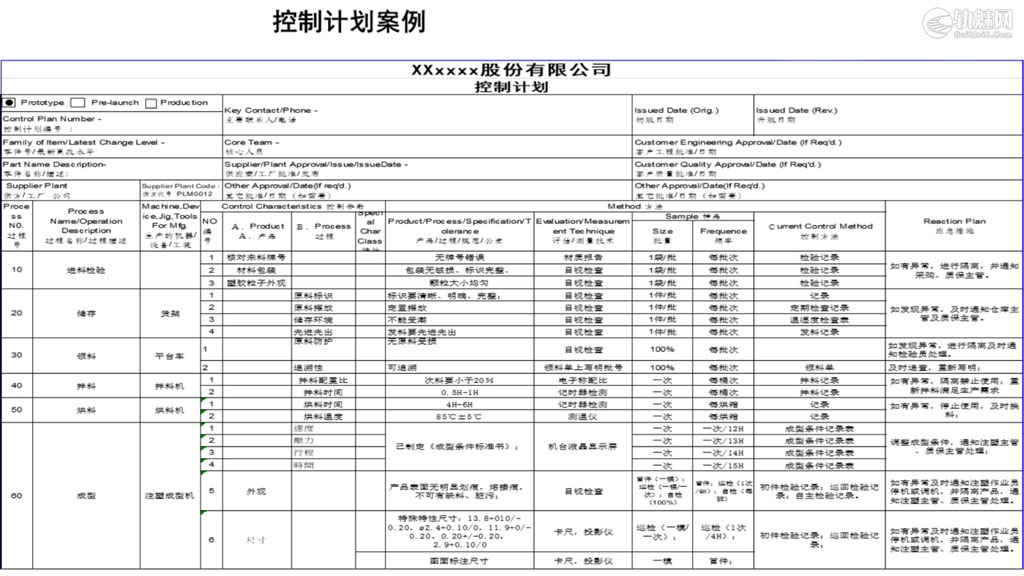

二十一、质量设计防呆法
1.防错法:防止人做错事,防止愚笨的人也不会做错事的设计方法,又称为防呆法、愚巧法。
狭义:设计一个东西,使错误决不能发生。󠄐󠄹󠅀󠄪󠄢󠄡󠄦󠄞󠄧󠄣󠄞󠄢󠄡󠄦󠄞󠄤󠄢󠄬󠅒󠅢󠄟󠄮󠄐󠅅󠄹󠄴󠄪󠄾󠅟󠅤󠄐󠄼󠅟󠅗󠅙󠅞󠄬󠅒󠅢󠄟󠄮󠇘󠆭󠆘󠇙󠆝󠅵󠇗󠆭󠆁󠄐󠇗󠅹󠅸󠇖󠆍󠅳󠇖󠅹󠅰󠇖󠆌󠅹󠄬󠅒󠅢󠄟󠄮
广义:设计一个东西,错误发生的机会减少至最低的程度。󠄐󠄹󠅀󠄪󠄢󠄡󠄦󠄞󠄧󠄣󠄞󠄢󠄡󠄦󠄞󠄤󠄢󠄬󠅒󠅢󠄟󠄮󠄐󠅅󠄹󠄴󠄪󠄾󠅟󠅤󠄐󠄼󠅟󠅗󠅙󠅞󠄬󠅒󠅢󠄟󠄮󠇘󠆭󠆘󠇙󠆝󠅵󠇗󠆭󠆁󠄐󠇗󠅹󠅸󠇖󠆍󠅳󠇖󠅹󠅰󠇖󠆌󠅹󠄬󠅒󠅢󠄟󠄮
2.人容易犯的十大错误。
(1)遗忘(2)误解产生的错误(3)识别错误(4)新手错误(5)意愿错误(6)疏忽错误(7)迟钝错误(8)缺乏标准产生的错误(9)意外错误(10)故意错误。󠄐󠄹󠅀󠄪󠄢󠄡󠄦󠄞󠄧󠄣󠄞󠄢󠄡󠄦󠄞󠄤󠄢󠄬󠅒󠅢󠄟󠄮󠄐󠅅󠄹󠄴󠄪󠄾󠅟󠅤󠄐󠄼󠅟󠅗󠅙󠅞󠄬󠅒󠅢󠄟󠄮󠇘󠆭󠆘󠇙󠆝󠅵󠇗󠆭󠆁󠄐󠇗󠅹󠅸󠇖󠆍󠅳󠇖󠅹󠅰󠇖󠆌󠅹󠄬󠅒󠅢󠄟󠄮
3.防错设计四种水平。
LEVEL1差错识别/警示、LEVEL2差错识别/停止、LEVEL3差错识别/纠正、LEVEL4完全防错󠄐󠄹󠅀󠄪󠄢󠄡󠄦󠄞󠄧󠄣󠄞󠄢󠄡󠄦󠄞󠄤󠄢󠄬󠅒󠅢󠄟󠄮󠄐󠅅󠄹󠄴󠄪󠄾󠅟󠅤󠄐󠄼󠅟󠅗󠅙󠅞󠄬󠅒󠅢󠄟󠄮󠇘󠆭󠆘󠇙󠆝󠅵󠇗󠆭󠆁󠄐󠇗󠅹󠅸󠇖󠆍󠅳󠇖󠅹󠅰󠇖󠆌󠅹󠄬󠅒󠅢󠄟󠄮
4.防错设计四大基本原则。
(1)使作业的动作轻松。(2)使作业不要技能与直觉。(3)使作业不会有危险。(4)使作业不依赖感官。󠄐󠄹󠅀󠄪󠄢󠄡󠄦󠄞󠄧󠄣󠄞󠄢󠄡󠄦󠄞󠄤󠄢󠄬󠅒󠅢󠄟󠄮󠄐󠅅󠄹󠄴󠄪󠄾󠅟󠅤󠄐󠄼󠅟󠅗󠅙󠅞󠄬󠅒󠅢󠄟󠄮󠇘󠆭󠆘󠇙󠆝󠅵󠇗󠆭󠆁󠄐󠇗󠅹󠅸󠇖󠆍󠅳󠇖󠅹󠅰󠇖󠆌󠅹󠄬󠅒󠅢󠄟󠄮
5.防错三大类别与十大原理技术。
(1)消除类:断根原理、自动原理、复制原理;
(2)控制类:保险原理、相符原理、顺序原理、隔离原理、缓和原理。
(3)警告类:层别原理、警告原理。
1.定义:
明白自己工作的各个步骤(5M+1E要素:人、机、料、法、环、测)的目的和意义 明步骤。󠄐󠄹󠅀󠄪󠄢󠄡󠄦󠄞󠄧󠄣󠄞󠄢󠄡󠄦󠄞󠄤󠄢󠄬󠅒󠅢󠄟󠄮󠄐󠅅󠄹󠄴󠄪󠄾󠅟󠅤󠄐󠄼󠅟󠅗󠅙󠅞󠄬󠅒󠅢󠄟󠄮󠇘󠆭󠆘󠇙󠆝󠅵󠇗󠆭󠆁󠄐󠇗󠅹󠅸󠇖󠆍󠅳󠇖󠅹󠅰󠇖󠆌󠅹󠄬󠅒󠅢󠄟󠄮
准备好工作的的必要的东西(设备、 工装、 材料) 备要件。󠄐󠄹󠅀󠄪󠄢󠄡󠄦󠄞󠄧󠄣󠄞󠄢󠄡󠄦󠄞󠄤󠄢󠄬󠅒󠅢󠄟󠄮󠄐󠅅󠄹󠄴󠄪󠄾󠅟󠅤󠄐󠄼󠅟󠅗󠅙󠅞󠄬󠅒󠅢󠄟󠄮󠇘󠆭󠆘󠇙󠆝󠅵󠇗󠆭󠆁󠄐󠇗󠅹󠅸󠇖󠆍󠅳󠇖󠅹󠅰󠇖󠆌󠅹󠄬󠅒󠅢󠄟󠄮
按规定的操作顺序标准进行作业守标准。󠄐󠄹󠅀󠄪󠄢󠄡󠄦󠄞󠄧󠄣󠄞󠄢󠄡󠄦󠄞󠄤󠄢󠄬󠅒󠅢󠄟󠄮󠄐󠅅󠄹󠄴󠄪󠄾󠅟󠅤󠄐󠄼󠅟󠅗󠅙󠅞󠄬󠅒󠅢󠄟󠄮󠇘󠆭󠆘󠇙󠆝󠅵󠇗󠆭󠆁󠄐󠇗󠅹󠅸󠇖󠆍󠅳󠇖󠅹󠅰󠇖󠆌󠅹󠄬󠅒󠅢󠄟󠄮
确认工作结果的良否后再交给下一工序验良否。󠄐󠄹󠅀󠄪󠄢󠄡󠄦󠄞󠄧󠄣󠄞󠄢󠄡󠄦󠄞󠄤󠄢󠄬󠅒󠅢󠄟󠄮󠄐󠅅󠄹󠄴󠄪󠄾󠅟󠅤󠄐󠄼󠅟󠅗󠅙󠅞󠄬󠅒󠅢󠄟󠄮󠇘󠆭󠆘󠇙󠆝󠅵󠇗󠆭󠆁󠄐󠇗󠅹󠅸󠇖󠆍󠅳󠇖󠅹󠅰󠇖󠆌󠅹󠄬󠅒󠅢󠄟󠄮
2.目的
要回到质量保证的原点, 以顾客的视角来明确应该做的事项,并脚踏实地去实行。󠄐󠄹󠅀󠄪󠄢󠄡󠄦󠄞󠄧󠄣󠄞󠄢󠄡󠄦󠄞󠄤󠄢󠄬󠅒󠅢󠄟󠄮󠄐󠅅󠄹󠄴󠄪󠄾󠅟󠅤󠄐󠄼󠅟󠅗󠅙󠅞󠄬󠅒󠅢󠄟󠄮󠇘󠆭󠆘󠇙󠆝󠅵󠇗󠆭󠆁󠄐󠇗󠅹󠅸󠇖󠆍󠅳󠇖󠅹󠅰󠇖󠆌󠅹󠄬󠅒󠅢󠄟󠄮
完成好交给自工序的工作, 不制造不良品, 不让不良品流到后工序。󠄐󠄹󠅀󠄪󠄢󠄡󠄦󠄞󠄧󠄣󠄞󠄢󠄡󠄦󠄞󠄤󠄢󠄬󠅒󠅢󠄟󠄮󠄐󠅅󠄹󠄴󠄪󠄾󠅟󠅤󠄐󠄼󠅟󠅗󠅙󠅞󠄬󠅒󠅢󠄟󠄮󠇘󠆭󠆘󠇙󠆝󠅵󠇗󠆭󠆁󠄐󠇗󠅹󠅸󠇖󠆍󠅳󠇖󠅹󠅰󠇖󠆌󠅹󠄬󠅒󠅢󠄟󠄮
3.意义
自工序完结,是制造质量目标得以实现的基础和前提。 依赖事后检查无法从根本上避免不良的流出。 只有通过自工序完结, 立足防止不良的发生, 才能防止不良流出车间, 防止不良流出工厂、 流入市场。󠄐󠄹󠅀󠄪󠄢󠄡󠄦󠄞󠄧󠄣󠄞󠄢󠄡󠄦󠄞󠄤󠄢󠄬󠅒󠅢󠄟󠄮󠄐󠅅󠄹󠄴󠄪󠄾󠅟󠅤󠄐󠄼󠅟󠅗󠅙󠅞󠄬󠅒󠅢󠄟󠄮󠇘󠆭󠆘󠇙󠆝󠅵󠇗󠆭󠆁󠄐󠇗󠅹󠅸󠇖󠆍󠅳󠇖󠅹󠅰󠇖󠆌󠅹󠄬󠅒󠅢󠄟󠄮
(1)自工序完结度(过程指标)󠄐󠄹󠅀󠄪󠄢󠄡󠄦󠄞󠄧󠄣󠄞󠄢󠄡󠄦󠄞󠄤󠄢󠄬󠅒󠅢󠄟󠄮󠄐󠅅󠄹󠄴󠄪󠄾󠅟󠅤󠄐󠄼󠅟󠅗󠅙󠅞󠄬󠅒󠅢󠄟󠄮󠇘󠆭󠆘󠇙󠆝󠅵󠇗󠆭󠆁󠄐󠇗󠅹󠅸󠇖󠆍󠅳󠇖󠅹󠅰󠇖󠆌󠅹󠄬󠅒󠅢󠄟󠄮
(2)后工序发现不良(结果指标)󠄐󠄹󠅀󠄪󠄢󠄡󠄦󠄞󠄧󠄣󠄞󠄢󠄡󠄦󠄞󠄤󠄢󠄬󠅒󠅢󠄟󠄮󠄐󠅅󠄹󠄴󠄪󠄾󠅟󠅤󠄐󠄼󠅟󠅗󠅙󠅞󠄬󠅒󠅢󠄟󠄮󠇘󠆭󠆘󠇙󠆝󠅵󠇗󠆭󠆁󠄐󠇗󠅹󠅸󠇖󠆍󠅳󠇖󠅹󠅰󠇖󠆌󠅹󠄬󠅒󠅢󠄟󠄮
“自工序完结度”(过程指标)与“后工序发现不良”(结果指标)在推进过程中相互确认, 最终到“自工序完结状态”。󠄐󠄹󠅀󠄪󠄢󠄡󠄦󠄞󠄧󠄣󠄞󠄢󠄡󠄦󠄞󠄤󠄢󠄬󠅒󠅢󠄟󠄮󠄐󠅅󠄹󠄴󠄪󠄾󠅟󠅤󠄐󠄼󠅟󠅗󠅙󠅞󠄬󠅒󠅢󠄟󠄮󠇘󠆭󠆘󠇙󠆝󠅵󠇗󠆭󠆁󠄐󠇗󠅹󠅸󠇖󠆍󠅳󠇖󠅹󠅰󠇖󠆌󠅹󠄬󠅒󠅢󠄟󠄮
4.改善推进步骤
(1)试点范围选定 (2)信息收集 (3)完结率初评 (4)差距/问题识别 (5)方案识别 (6)改善确认 (7)标准建立 (8)培训及确认 (9)监督及反馈 (10)完结率再评 (11)员工改善提案 (12)OPL (13)变化点管理 (14)目视化管理。󠄐󠄹󠅀󠄪󠄢󠄡󠄦󠄞󠄧󠄣󠄞󠄢󠄡󠄦󠄞󠄤󠄢󠄬󠅒󠅢󠄟󠄮󠄐󠅅󠄹󠄴󠄪󠄾󠅟󠅤󠄐󠄼󠅟󠅗󠅙󠅞󠄬󠅒󠅢󠄟󠄮󠇘󠆭󠆘󠇙󠆝󠅵󠇗󠆭󠆁󠄐󠇗󠅹󠅸󠇖󠆍󠅳󠇖󠅹󠅰󠇖󠆌󠅹󠄬󠅒󠅢󠄟󠄮