随着城市规模不断扩大、城市人口日益激增、1城市机动车拥有数量迅速增长,污染和耗能问题以及城市道路的拥堵问题成为制约城市发展的症结。而城市轨道交通以低污染、低能耗、大容量及安全、准时、快速的优点成为解决城市交通问题的首选方案。地铁轨道工程作为土建和机电安装承上启下的工程,对地铁能否按期投入运营起着至关重要的作用。十几年来,传统的地铁整体道床轨道施工均采用人工精调轨道、现场浇筑混凝土方式,存在施工进度缓慢、混凝土现浇质量控制难、劳动强度大、作业环境恶劣等诸多弊端。随着结构设计复杂的减振降噪技术在轨道工程中的应用,传统的现场浇筑混凝土道床施工模式,还存在施工效率低下、质量控制难,影响减振效果的问题。󠄐󠄹󠅀󠄪󠄢󠄡󠄦󠄞󠄧󠄣󠄞󠄢󠄡󠄦󠄞󠄡󠄦󠄩󠄬󠅒󠅢󠄟󠄮󠄐󠅅󠄹󠄴󠄪󠄾󠅟󠅤󠄐󠄼󠅟󠅗󠅙󠅞󠄬󠅒󠅢󠄟󠄮󠇘󠆭󠆘󠇙󠆝󠅵󠇗󠆭󠆁󠄐󠇗󠅹󠅸󠇖󠆍󠅳󠇖󠅹󠅰󠇖󠆌󠅹󠄬󠅒󠅢󠄟󠄮
为了适应地铁在各大城市的大规模建设,急需克服现有地铁轨道施工技术瓶颈,将高速铁路成熟的精密测量技术及板式轨道技术引入地铁,开展相关技术研究。󠄐󠄹󠅀󠄪󠄢󠄡󠄦󠄞󠄧󠄣󠄞󠄢󠄡󠄦󠄞󠄡󠄦󠄩󠄬󠅒󠅢󠄟󠄮󠄐󠅅󠄹󠄴󠄪󠄾󠅟󠅤󠄐󠄼󠅟󠅗󠅙󠅞󠄬󠅒󠅢󠄟󠄮󠇘󠆭󠆘󠇙󠆝󠅵󠇗󠆭󠆁󠄐󠇗󠅹󠅸󠇖󠆍󠅳󠇖󠅹󠅰󠇖󠆌󠅹󠄬󠅒󠅢󠄟󠄮
1 地铁预制板式轨道提出的背景
近年来,随着建筑工业化模式的不断发展,国内在预制混凝土装配式建筑方面的研究与应用逐渐升温,预制混凝土装配式结构在建筑施工质量、节能减排效果、综合经济效益等多方面具有优于现浇混凝土结构的性能。轨道交通建设作为建筑业的一个分支和国内新兴产业,其在今后一段时间将处于空前的发展阶段,在新形势下,适应市场形势和产业发展的要求,需不断创新发展提升轨道交通建设和管理水平。
随着国内高速铁路板式轨道的快速发展和先进的测量控制技术手段的使用,为地铁轨道工程的施工和发展提供了一个全新的思路和模式。但是地铁轨道不同于高速铁路,在设计技术标准、工况边界条件、环境减振降噪需求等方面存在着差异。其技术能否在地铁施工中运用,需结合地铁轨道施工的特点,在消化吸收高速铁路轨道施工技术的基础上,克服轨道基础控制网测量、数字化精调、狭窄环境机械化装配等技术瓶颈,形成一套新的地铁预制板轨道施工工艺工法和配套工装。󠄐󠄹󠅀󠄪󠄢󠄡󠄦󠄞󠄧󠄣󠄞󠄢󠄡󠄦󠄞󠄡󠄦󠄩󠄬󠅒󠅢󠄟󠄮󠄐󠅅󠄹󠄴󠄪󠄾󠅟󠅤󠄐󠄼󠅟󠅗󠅙󠅞󠄬󠅒󠅢󠄟󠄮󠇘󠆭󠆘󠇙󠆝󠅵󠇗󠆭󠆁󠄐󠇗󠅹󠅸󠇖󠆍󠅳󠇖󠅹󠅰󠇖󠆌󠅹󠄬󠅒󠅢󠄟󠄮
为此,借鉴高速铁路自主知识产权的CRTSⅢ型板式无砟轨道技术[1],上海地铁尝试在12号线设计了370m普通预制板轨道。为了顺利完成该工程项目,为地铁预制板轨道施工积累经验,提出论文以供研究。
2 主要研究内容
以上海地铁12号线项目为依托,配合设计院提出预制轨道设计总体方案,结合地铁隧道结构限界特点、小半径线形特征及目前地铁铺轨工装配置能力,分析预制轨道板采用的板型,开展地铁预制板轨道施工技术研究,研发出配套的板式轨道测量及施工工法,系统解决新型地铁板式轨道施工难题。
1)针对地铁限界尺寸,从施工角度对地铁预制板的结构尺寸进行分析,结合现有铺板工装能力,设计预制板长度、吊装位置、轨道板三向调整器安装位置等,提出系统化的预制板轨道设计-施工一体化解决方案。󠄐󠄹󠅀󠄪󠄢󠄡󠄦󠄞󠄧󠄣󠄞󠄢󠄡󠄦󠄞󠄡󠄦󠄩󠄬󠅒󠅢󠄟󠄮󠄐󠅅󠄹󠄴󠄪󠄾󠅟󠅤󠄐󠄼󠅟󠅗󠅙󠅞󠄬󠅒󠅢󠄟󠄮󠇘󠆭󠆘󠇙󠆝󠅵󠇗󠆭󠆁󠄐󠇗󠅹󠅸󠇖󠆍󠅳󠇖󠅹󠅰󠇖󠆌󠅹󠄬󠅒󠅢󠄟󠄮
2)消化吸收高速铁路CPⅢ轨道控制网测量技术,根据地铁测量的特点,进行系统的理论精度分析及现场验证,将精密测量技术应用于地铁轨道几何尺寸的调整和预制轨道板的精调。󠄐󠄹󠅀󠄪󠄢󠄡󠄦󠄞󠄧󠄣󠄞󠄢󠄡󠄦󠄞󠄡󠄦󠄩󠄬󠅒󠅢󠄟󠄮󠄐󠅅󠄹󠄴󠄪󠄾󠅟󠅤󠄐󠄼󠅟󠅗󠅙󠅞󠄬󠅒󠅢󠄟󠄮󠇘󠆭󠆘󠇙󠆝󠅵󠇗󠆭󠆁󠄐󠇗󠅹󠅸󠇖󠆍󠅳󠇖󠅹󠅰󠇖󠆌󠅹󠄬󠅒󠅢󠄟󠄮
3)在消化吸收高速铁路板式道床施工经验的基础上,结合地铁施工工况条件及施工技术特点,研发适用于地铁施工的普通预制板轨道施工工艺及配套工装设备。󠄐󠄹󠅀󠄪󠄢󠄡󠄦󠄞󠄧󠄣󠄞󠄢󠄡󠄦󠄞󠄡󠄦󠄩󠄬󠅒󠅢󠄟󠄮󠄐󠅅󠄹󠄴󠄪󠄾󠅟󠅤󠄐󠄼󠅟󠅗󠅙󠅞󠄬󠅒󠅢󠄟󠄮󠇘󠆭󠆘󠇙󠆝󠅵󠇗󠆭󠆁󠄐󠇗󠅹󠅸󠇖󠆍󠅳󠇖󠅹󠅰󠇖󠆌󠅹󠄬󠅒󠅢󠄟󠄮
3 地铁轨道控制网的设计及应用
对于地铁板式轨道,如果采用传统的基标测量方法,其定位精度难以保证,且调板效率低,而采用高速铁路CPⅢ轨道控制网测量技术,则可实现轨道板数字化精调,提高精调效率和质量。
高速铁路CPⅢ轨道控制网的特点是控制点沿线路布置在路基两侧的接触网杆或基础、桥梁防撞墙、隧道侧壁上,点间距为纵向60m左右,可供双线使用,测量精度为相邻点位的相对点位中误差小于1mm[2]。
而地铁隧道相比高速铁路,隧道大部分为单线隧道、曲线半径小,且频繁交错布置,隧道壁上布置有疏散平台、电缆支架、消防水管等,设置条件很差,视线不良。直接采用高速铁路CPⅢ控制网布设测量的方法,将无法满足点位的测量及保护要求,需对其布设间距、高度等进行针对性的布网设计。󠄐󠄹󠅀󠄪󠄢󠄡󠄦󠄞󠄧󠄣󠄞󠄢󠄡󠄦󠄞󠄡󠄦󠄩󠄬󠅒󠅢󠄟󠄮󠄐󠅅󠄹󠄴󠄪󠄾󠅟󠅤󠄐󠄼󠅟󠅗󠅙󠅞󠄬󠅒󠅢󠄟󠄮󠇘󠆭󠆘󠇙󠆝󠅵󠇗󠆭󠆁󠄐󠇗󠅹󠅸󠇖󠆍󠅳󠇖󠅹󠅰󠇖󠆌󠅹󠄬󠅒󠅢󠄟󠄮
通过现场反复试验,对测量数据对比,提出地铁轨道基础控制点沿线路成对布设的方案,技术要求如表1所示。受地铁小半径曲线的限制条件,曲线地段一般在30~45m成对布设[3],满足通视条件。
控制点布设时根据限界图中线路设备的设计位置进行综合比选,选择结构稳定、高度合适、便于控制网测量的位置进行布点。单圆隧道区间段左侧控制点布设在侧向平台以上10cm位置,距轨面约1.2m;右侧控制点布设在给水管与区间电话箱之间侧墙上,距轨面约1.1m。
4 地铁预制板式轨道设计
国内先后在京津、哈大、京沪、郑徐等高速铁路大量采用板式无砟轨道,其雏形主要来源于德国博格板和日本框架板,后通过消化吸收再创新,设计出自主知识产权的CRTSⅢ型板式无砟轨道,具有施工方便、成本较国外引入低的优势,通过工程实践,总结出了成套施工技术和配套工装。其显著特点是将大量现场浇筑混凝土作业转入工厂化预制,这对地铁项目将有很好的可借鉴性,能够解决地铁作业环境狭窄的问题,并为地铁养护维修提供便利条件,为此,尝试将高速铁路CRTSⅢ型板式轨道引入地铁,结合地铁工况条件进行设计,开发配套的施工工艺和工装。
.png)
图1 板式轨道结构三维示意(俯视图)
.png)
图2 板式轨道结构三维示意(仰视图)
根据高速铁路板式轨道结构,结合地铁工况条件,设计地铁的普通预制板轨道。其结构由钢轨、扣件、预制轨道板、自密实混凝土充填层、限位结构(门型筋+凹槽)、中间隔离层(土工布隔离层)和钢筋混凝土基底组成[4],其三维模拟示意如图1、图2。单块预制轨道板重约6t。
1)轨道板。轨道板采用单元分块式结构,为无挡肩钢筋混凝土结构,混凝土强度等级为C50,非预应力结构,设计轨道板纵向长度4700mm,宽度2300mm,厚度为200mm,轨底坡设于板上。板间设置100mm板缝,扣件间距600mm。扣件安装位置设置420mm×290mm承轨台,钢轨中心位置承轨台高度25mm,1/40轨底坡设置于承轨台。每块板留置3个注浆/排气孔,上口直径160mm,下口直径140mm。󠄐󠄹󠅀󠄪󠄢󠄡󠄦󠄞󠄧󠄣󠄞󠄢󠄡󠄦󠄞󠄡󠄦󠄩󠄬󠅒󠅢󠄟󠄮󠄐󠅅󠄹󠄴󠄪󠄾󠅟󠅤󠄐󠄼󠅟󠅗󠅙󠅞󠄬󠅒󠅢󠄟󠄮󠇘󠆭󠆘󠇙󠆝󠅵󠇗󠆭󠆁󠄐󠇗󠅹󠅸󠇖󠆍󠅳󠇖󠅹󠅰󠇖󠆌󠅹󠄬󠅒󠅢󠄟󠄮
2)自密实混凝土充填层。轨道板与基底间设置自密实混凝土,即自密实混凝土结构调整层,强度等级为C35,厚度为80mm,采用单层钢筋网配筋设置。󠄐󠄹󠅀󠄪󠄢󠄡󠄦󠄞󠄧󠄣󠄞󠄢󠄡󠄦󠄞󠄡󠄦󠄩󠄬󠅒󠅢󠄟󠄮󠄐󠅅󠄹󠄴󠄪󠄾󠅟󠅤󠄐󠄼󠅟󠅗󠅙󠅞󠄬󠅒󠅢󠄟󠄮󠇘󠆭󠆘󠇙󠆝󠅵󠇗󠆭󠆁󠄐󠇗󠅹󠅸󠇖󠆍󠅳󠇖󠅹󠅰󠇖󠆌󠅹󠄬󠅒󠅢󠄟󠄮
3)中间隔离层(土工布隔离层)。自密实混凝土与基底间设置中间隔离层,采用4mm聚丙烯无纺土工布。󠄐󠄹󠅀󠄪󠄢󠄡󠄦󠄞󠄧󠄣󠄞󠄢󠄡󠄦󠄞󠄡󠄦󠄩󠄬󠅒󠅢󠄟󠄮󠄐󠅅󠄹󠄴󠄪󠄾󠅟󠅤󠄐󠄼󠅟󠅗󠅙󠅞󠄬󠅒󠅢󠄟󠄮󠇘󠆭󠆘󠇙󠆝󠅵󠇗󠆭󠆁󠄐󠇗󠅹󠅸󠇖󠆍󠅳󠇖󠅹󠅰󠇖󠆌󠅹󠄬󠅒󠅢󠄟󠄮
4)基底。基底为钢筋混凝土结构,强度等级为C35。󠄐󠄹󠅀󠄪󠄢󠄡󠄦󠄞󠄧󠄣󠄞󠄢󠄡󠄦󠄞󠄡󠄦󠄩󠄬󠅒󠅢󠄟󠄮󠄐󠅅󠄹󠄴󠄪󠄾󠅟󠅤󠄐󠄼󠅟󠅗󠅙󠅞󠄬󠅒󠅢󠄟󠄮󠇘󠆭󠆘󠇙󠆝󠅵󠇗󠆭󠆁󠄐󠇗󠅹󠅸󠇖󠆍󠅳󠇖󠅹󠅰󠇖󠆌󠅹󠄬󠅒󠅢󠄟󠄮
5)限位结构。轨道板下设门型筋,基底采用双凹槽方案,凹槽长×宽×深:700mm×400mm×80mm。󠄐󠄹󠅀󠄪󠄢󠄡󠄦󠄞󠄧󠄣󠄞󠄢󠄡󠄦󠄞󠄡󠄦󠄩󠄬󠅒󠅢󠄟󠄮󠄐󠅅󠄹󠄴󠄪󠄾󠅟󠅤󠄐󠄼󠅟󠅗󠅙󠅞󠄬󠅒󠅢󠄟󠄮󠇘󠆭󠆘󠇙󠆝󠅵󠇗󠆭󠆁󠄐󠇗󠅹󠅸󠇖󠆍󠅳󠇖󠅹󠅰󠇖󠆌󠅹󠄬󠅒󠅢󠄟󠄮
6)扣件。采用DTIII-2A型扣件,该扣件为配合板式道床设计,新研发的大调整量扣件,单个扣件底板调整量为–10~+12mm。󠄐󠄹󠅀󠄪󠄢󠄡󠄦󠄞󠄧󠄣󠄞󠄢󠄡󠄦󠄞󠄡󠄦󠄩󠄬󠅒󠅢󠄟󠄮󠄐󠅅󠄹󠄴󠄪󠄾󠅟󠅤󠄐󠄼󠅟󠅗󠅙󠅞󠄬󠅒󠅢󠄟󠄮󠇘󠆭󠆘󠇙󠆝󠅵󠇗󠆭󠆁󠄐󠇗󠅹󠅸󠇖󠆍󠅳󠇖󠅹󠅰󠇖󠆌󠅹󠄬󠅒󠅢󠄟󠄮
7)轨道结构高度情况。轨道结构各部位结构尺寸:176mm(钢轨)+38mm(扣件高度)+25mm(承轨台)+200mm(轨道板厚度)+80mm(自密实混凝土层厚度)+4mm(土工布隔离层)+212mm(隧道仰拱理论基底中心高度)=735mm。如图3所示。󠄐󠄹󠅀󠄪󠄢󠄡󠄦󠄞󠄧󠄣󠄞󠄢󠄡󠄦󠄞󠄡󠄦󠄩󠄬󠅒󠅢󠄟󠄮󠄐󠅅󠄹󠄴󠄪󠄾󠅟󠅤󠄐󠄼󠅟󠅗󠅙󠅞󠄬󠅒󠅢󠄟󠄮󠇘󠆭󠆘󠇙󠆝󠅵󠇗󠆭󠆁󠄐󠇗󠅹󠅸󠇖󠆍󠅳󠇖󠅹󠅰󠇖󠆌󠅹󠄬󠅒󠅢󠄟󠄮
5 铺设总体方案及工装配置
5.1 铺板总体方案
轨道板采用工厂化预制生产,加工成型的成品轨道板通过汽车运输至铺轨基地存储,在铺轨基地内采用桁车将预制轨道板吊装至平板车上,轨道车运输至作业面,隧道内施工作业面采用轨行式铺轨门吊进行轨道板吊运、铺设作业,采用轨道基础控制网及配套测量系统及工装设备进行轨道板几何位置调整,固定轨道板位置后进行自密实混凝土层的灌注施工,安装线路钢轨扣件等作业。
地铁普通道床板式轨道施工基本工艺流程如图4所示。󠄐󠄹󠅀󠄪󠄢󠄡󠄦󠄞󠄧󠄣󠄞󠄢󠄡󠄦󠄞󠄡󠄦󠄩󠄬󠅒󠅢󠄟󠄮󠄐󠅅󠄹󠄴󠄪󠄾󠅟󠅤󠄐󠄼󠅟󠅗󠅙󠅞󠄬󠅒󠅢󠄟󠄮󠇘󠆭󠆘󠇙󠆝󠅵󠇗󠆭󠆁󠄐󠇗󠅹󠅸󠇖󠆍󠅳󠇖󠅹󠅰󠇖󠆌󠅹󠄬󠅒󠅢󠄟󠄮
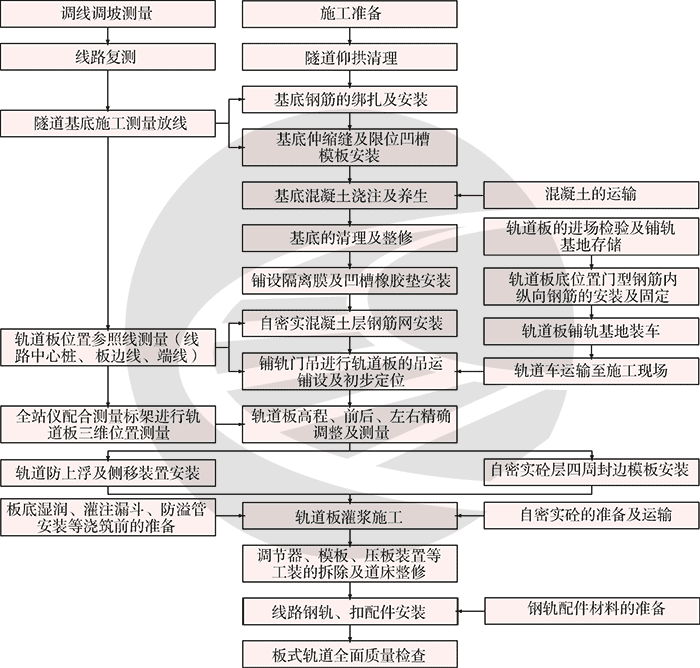
图4 地铁普通预制板轨道施工基本工艺流程
5.2 工装配置
除基底钢筋加工、混凝土浇筑所需常规设备外,还需配置轨道板运输、铺设、精调成套工装,部分工装需要结合具体工况研制,主要工装配置见表2。
表2 铺板主要工装配置
设备名称 | 规格型号 | 用途 |
桁架式龙门吊 | 10t | 基地吊装轨道板 |
地铁专用轨道车 | JY-290 | 轨道板及材料运输 |
地铁专用轨道平车 | PD25 | 轨道板及材料运输 |
地铁轨道铺设机 | 轨行式,额定起重量12000kg | 轨道板洞内吊装、铺设 |
轮胎式轨道板运输车 | 轮胎走行,装载质量15000kg | 轨道板无轨运输 |
三向调节器 | 新研制 | 轨道板精调 |
反力架 | 新研制 | 轨道板精调后固定 |
自密实混凝土灌注料斗及溜槽 | 新研制 | 自密实混凝土灌注 |
全站仪 | TCRA1201R100,1″ | 控制网测量,轨道板精调测量 |
轨道板测量标架及配套调板软件 | 测量标架为螺栓孔适配形式 | 轨道板精调 |
轨道几何状态测量仪 | 安伯格GRP-1000S | 轨道精调 |
6 铺设工艺及技术要求
6.1 基底施工
根据调线调坡后的线路,测设线路中心线、板缝位置线、基底高程控制桩,作为基底钢筋网绑扎、结构缝设置里程、限位凹槽设置位置、基底混凝土高程控制的基准。
特别要重视基底限位凹槽模板的安装,直线地段限位凹槽中心位置同线路中心线,曲线地段限位凹槽中心位置同线路中心存在理论偏移,需根据超高计算理论偏移值,见式1。󠄐󠄹󠅀󠄪󠄢󠄡󠄦󠄞󠄧󠄣󠄞󠄢󠄡󠄦󠄞󠄡󠄦󠄩󠄬󠅒󠅢󠄟󠄮󠄐󠅅󠄹󠄴󠄪󠄾󠅟󠅤󠄐󠄼󠅟󠅗󠅙󠅞󠄬󠅒󠅢󠄟󠄮󠇘󠆭󠆘󠇙󠆝󠅵󠇗󠆭󠆁󠄐󠇗󠅹󠅸󠇖󠆍󠅳󠇖󠅹󠅰󠇖󠆌󠅹󠄬󠅒󠅢󠄟󠄮
d=H×tg(arcsin(Δh/1500))(1)
式中:均按mm取值;d为板式轨道顶板凹槽中心线同轨道中心线的偏离值;H为板式道床轨顶面至基底表面的高差,按道床设计523取值;Δh为外轨超高值;
1500为左右股钢轨轨顶面距离。󠄐󠄹󠅀󠄪󠄢󠄡󠄦󠄞󠄧󠄣󠄞󠄢󠄡󠄦󠄞󠄡󠄦󠄩󠄬󠅒󠅢󠄟󠄮󠄐󠅅󠄹󠄴󠄪󠄾󠅟󠅤󠄐󠄼󠅟󠅗󠅙󠅞󠄬󠅒󠅢󠄟󠄮󠇘󠆭󠆘󠇙󠆝󠅵󠇗󠆭󠆁󠄐󠇗󠅹󠅸󠇖󠆍󠅳󠇖󠅹󠅰󠇖󠆌󠅹󠄬󠅒󠅢󠄟󠄮
6.2 轨道板位置测量放线及曲线布板
为了给轨道板初步就位、铺设土工布、自密实混凝土层钢筋网片绑扎提供基准位置,需进行轨道板位置的测量放线。地铁轨道板的设计板型均为标准的直线板,均按直线板进行预制,曲线地段需“以直代曲”,采用“半矢法”进行布板,施工测量放线时,应注意轨道板中心线同线路中心线的几何关系。
6.3 隔离层及弹性垫层铺设
土工布铺设前应将底座表面和限位凹槽清理干净,土工布铺设较轨道板四周边缘宽出50mm(轨道板2300mm宽,土工布2400mm宽)[5],卷材沿轨道线路方向,摊开进行铺设。
6.4 钢筋网片铺设
铺设钢筋网片以线路中心线为基准,进行钢筋网片的铺设。部分钢筋在轨道板板底门形筋位置穿纵向钢筋,按设计要求进行设置。
6.5 轨道板存储、运输及铺设
为了避免轨道板存储变形,轨道板存储的场地及台位需进行混凝土硬化,硬化的场地应平整,存储轨道板时,板底及每层间隔设置专用支撑垫木。存放层高不宜大于5层。单块轨道板约6t,当存储场地位于车站顶板上时,还应满足车站顶板荷载的要求。
在铺轨基地利用门式起重机将预制道床板由铺轨基地轨排孔吊装至平板车上,每辆PD25型平板车装4块轨道板(双层布置,板底设置支撑垫木)。轨道车牵引平板车,运输至铺设作业面。󠄐󠄹󠅀󠄪󠄢󠄡󠄦󠄞󠄧󠄣󠄞󠄢󠄡󠄦󠄞󠄡󠄦󠄩󠄬󠅒󠅢󠄟󠄮󠄐󠅅󠄹󠄴󠄪󠄾󠅟󠅤󠄐󠄼󠅟󠅗󠅙󠅞󠄬󠅒󠅢󠄟󠄮󠇘󠆭󠆘󠇙󠆝󠅵󠇗󠆭󠆁󠄐󠇗󠅹󠅸󠇖󠆍󠅳󠇖󠅹󠅰󠇖󠆌󠅹󠄬󠅒󠅢󠄟󠄮
轨道板铺设前,应预先在基底表面放置支撑垫木,垫木位置应放在轨道板板端位置,放置4块垫木做临时支撑(垫木放置位置宜临边,在调节器起板后方便取出)。垫木高度按70mm厚度加工(小于自密实混凝土层厚度,道床板自密实混凝土设计厚度80mm)[6]。
作业面铺轨门吊配合进行轨道板的铺设,以放样的边线和板缝线为基准进行落板并初步就位,轨道粗铺精度控制:前后允许偏差10mm,左右允许偏差10mm[7],满足后续轨道板精调时调节器的调节范围要求。
6.6 轨道板精调及固定
轨道板初步铺设后,四角安装三向调节器,注意调节器与基底间设置支撑垫木(宜采用硬杂木),首先将高程调节螺栓调节处于最低位置,左右前后调节螺栓调节处于中间位置。注意安装调节器前,需将两侧封边模板临时安装到位(调节器临近轨道板,安装完毕后两侧模板无法安装)。
轨道板上利用扣件尼龙套管作为棱镜定位孔,全站仪实时测量同棱镜交换数据,指挥人工利用三向调节器进行轨道板的精调。轨道板精调注意搭接测量,避免产生累积偏差。精调过程中应注意四角步调一致,避免单点受力过大造成轨道板吊装孔处边角破损,精调允许偏差如表3[8]。轨道板精调完毕后,应检查四角位置的调节器是否均处于受力状态(可能存在精调器三点受力状态,造成轨道板固定不牢固)。
在缓和曲线调板时,缓和曲线地段因理论上两股钢轨为扭曲面,曲线外股以低点(直线方向的点位)控制轨道板的高程,按坡度进行叠加。󠄐󠄹󠅀󠄪󠄢󠄡󠄦󠄞󠄧󠄣󠄞󠄢󠄡󠄦󠄞󠄡󠄦󠄩󠄬󠅒󠅢󠄟󠄮󠄐󠅅󠄹󠄴󠄪󠄾󠅟󠅤󠄐󠄼󠅟󠅗󠅙󠅞󠄬󠅒󠅢󠄟󠄮󠇘󠆭󠆘󠇙󠆝󠅵󠇗󠆭󠆁󠄐󠇗󠅹󠅸󠇖󠆍󠅳󠇖󠅹󠅰󠇖󠆌󠅹󠄬󠅒󠅢󠄟󠄮
轨道板精调完毕后,安装四周封边模板(即两侧及端头封边模板)、轨道板防上浮支架(反力架),曲线地段还需安装防侧向位移支架。󠄐󠄹󠅀󠄪󠄢󠄡󠄦󠄞󠄧󠄣󠄞󠄢󠄡󠄦󠄞󠄡󠄦󠄩󠄬󠅒󠅢󠄟󠄮󠄐󠅅󠄹󠄴󠄪󠄾󠅟󠅤󠄐󠄼󠅟󠅗󠅙󠅞󠄬󠅒󠅢󠄟󠄮󠇘󠆭󠆘󠇙󠆝󠅵󠇗󠆭󠆁󠄐󠇗󠅹󠅸󠇖󠆍󠅳󠇖󠅹󠅰󠇖󠆌󠅹󠄬󠅒󠅢󠄟󠄮
表3 轨道板精调定位允许偏差
检查项目 | 允许偏差/mm |
高程 | ±0.5 |
中线 | 0.5 |
前后 | ±5 |
相邻轨道板接缝处承轨台顶面相对高差 | 0.3 |
相邻轨道板接缝处承轨台顶面平面位置 | 0.3 |
6.7板下自密实混凝土灌注
目前地铁普通道床施工均采用商品混凝土,板式道床自密实混凝土同浇筑道床的混凝土不同,单次使用数量少,材料质量要求严,混凝土配置质量控制要求高,地铁铺轨位于市区,商品混凝土厂家一般距离铺轨基地较远,运输至铺轨基地后还需轨道车运输至作业面,拌制到浇筑的时间长且不易控制,无法满足自密实混凝土的施工要求。为了自密实混凝土的拌制,需在铺轨基地设置小型搅拌站,采用小型搅拌设备进行混凝土的集中拌制。在上海地铁17号线施工时,自密实混凝土用量较大,采用商品混凝土。
自密实混凝土其配合比设计及相关揭板试验参照高速铁路CRTSⅢ型板施工进行。严格按照揭板试验材料配合比配料,每块板自密实混凝土方量约1.2m3,按照浇筑板的数量确定拌制方量,并稍有富余。
灌注时,宜采用“慢-快-慢”方式[9],连续一次性完成单块板的灌注,单块板灌注时间宜控制在10~15min。防溢管在自密实混凝土混凝土浇筑完成3h后拔除,并在板面预留孔位置插入S型钩筋,进行灌注口(或防溢孔)的混凝土收面。调节器及压板支架应在自密实混凝土终凝后拆除。轨道板上堆积重物及承受振动冲击荷载时,需注意混凝土龄期同强度的关系,必要时做抗压强度试压,合理确定承受荷载时间。
6.8 钢轨扣件安装及轨道精调
按照设计图纸进行扣件安装,铺设钢轨,形成临时线路。扣件安装完毕后,对轨道几何尺寸进行检查,确保工程列车的安全运行。
地铁轨道板的设计均为标准的直线板,按直线板预制,曲线地段需“以直代曲”,采用“半矢法”,即第二组扣件中心线处线路中心线与板中心线偏离值为0,其余扣件中心线处矢距通过扣件调整,DTⅢ2-A扣件轨距调节量:单个扣件底板调整量为–10~+12mm,在保证工务维修量的情况下,满足施工技术的要求。󠄐󠄹󠅀󠄪󠄢󠄡󠄦󠄞󠄧󠄣󠄞󠄢󠄡󠄦󠄞󠄡󠄦󠄩󠄬󠅒󠅢󠄟󠄮󠄐󠅅󠄹󠄴󠄪󠄾󠅟󠅤󠄐󠄼󠅟󠅗󠅙󠅞󠄬󠅒󠅢󠄟󠄮󠇘󠆭󠆘󠇙󠆝󠅵󠇗󠆭󠆁󠄐󠇗󠅹󠅸󠇖󠆍󠅳󠇖󠅹󠅰󠇖󠆌󠅹󠄬󠅒󠅢󠄟󠄮
7 应用实例及效果
本文阐述的地铁轨道基础控制网测量技术目前在上海、北京、杭州、宁波、厦门、武汉、深圳、西安等城市的地铁轨道工程均得到了推广应用。上海地铁尝试在12号线设计了370m普通预制板轨道,该线路于2015年12月19日运营通车,列车运行平稳安全,继上海地铁12号线后,上海轨道17号线公司标段总长3.8km应用了该型板式道床,受土建工期滞后1个月影响,铺轨基地不能移交,导致预制轨道板及其他材料无法按计划储备,不能提前进行基底施工,两端下料口仅单侧预留,增大了基底混凝土输送难度,后续轨道板铺设受轨道板材料供应影响,综合进度指标约40m/d,没能达到预期的75m/d。轨道板精调精度能够控制在规定范围内,施工过程中虽然采取了轨道板固定工装,但曲线地段仍有上浮和侧移,自密实混凝土灌注后安装钢轨,需对轨道几何尺寸进行精调,轨道精调后局部地段无砟轨道竣工测量数据见表4。
表4 无砟轨道竣工测量几何尺寸数据
里程 | 轨距偏差 | 平面偏差 | 轨面高程偏差 | 超高偏差 |
SK8+925.041 | 0.4 | 0.0 | 0.0 | 0.0 |
SK8+929.367 | –0.5 | –0.4 | –0.3 | 0.4 |
SK8+933.546 | 0.0 | 0.7 | –0.4 | –0.7 |
SK8+937.823 | 0.0 | 0.9 | 0.2 | –0.9 |
SK8+942.076 | 0.3 | 0.4 | 0.4 | –0.4 |
SK8+946.328 | –0.4 | 0.4 | 0.1 | –0.4 |
SK8+950.581 | 0.4 | –1.3 | 0.2 | 1.3 |
SK8+954.833 | –0.2 | 1.5 | 0.2 | 0.3 |
SK8+959.086 | –0.2 | –0.1 | 0.6 | 0.4 |
SK8+963.338 | 0.3 | 0.6 | –0.7 | 0.3 |
随着地铁测量基础控制网技术的攻克,为地铁预制板轨道数字化精调提供了条件。如果大量推广使用,还需结合地铁具体工况和施工组织,不断研究,进一步改进工装配备,优化工艺工法,以期达到预期工效目标。采用板式轨道结构提高了轨道的可维修性、可更换性,有效地降低后期运营维护成本。尤其针对特殊不良地质条件下,对地铁道床的整修更换、处理,提供了可行性和更为便利的条件。
文章来源:
原文名称:板式轨道在地铁中的应用研究󠄐󠄹󠅀󠄪󠄢󠄡󠄦󠄞󠄧󠄣󠄞󠄢󠄡󠄦󠄞󠄡󠄦󠄩󠄬󠅒󠅢󠄟󠄮󠄐󠅅󠄹󠄴󠄪󠄾󠅟󠅤󠄐󠄼󠅟󠅗󠅙󠅞󠄬󠅒󠅢󠄟󠄮󠇘󠆭󠆘󠇙󠆝󠅵󠇗󠆭󠆁󠄐󠇗󠅹󠅸󠇖󠆍󠅳󠇖󠅹󠅰󠇖󠆌󠅹󠄬󠅒󠅢󠄟󠄮
作者信息:曹德志(中铁一局集团新运工程有限公司,陕西咸阳 712000)󠄐󠄹󠅀󠄪󠄢󠄡󠄦󠄞󠄧󠄣󠄞󠄢󠄡󠄦󠄞󠄡󠄦󠄩󠄬󠅒󠅢󠄟󠄮󠄐󠅅󠄹󠄴󠄪󠄾󠅟󠅤󠄐󠄼󠅟󠅗󠅙󠅞󠄬󠅒󠅢󠄟󠄮󠇘󠆭󠆘󠇙󠆝󠅵󠇗󠆭󠆁󠄐󠇗󠅹󠅸󠇖󠆍󠅳󠇖󠅹󠅰󠇖󠆌󠅹󠄬󠅒󠅢󠄟󠄮
期刊信息:都市快轨交通· 2018 年2 月󠄐󠄹󠅀󠄪󠄢󠄡󠄦󠄞󠄧󠄣󠄞󠄢󠄡󠄦󠄞󠄡󠄦󠄩󠄬󠅒󠅢󠄟󠄮󠄐󠅅󠄹󠄴󠄪󠄾󠅟󠅤󠄐󠄼󠅟󠅗󠅙󠅞󠄬󠅒󠅢󠄟󠄮󠇘󠆭󠆘󠇙󠆝󠅵󠇗󠆭󠆁󠄐󠇗󠅹󠅸󠇖󠆍󠅳󠇖󠅹󠅰󠇖󠆌󠅹󠄬󠅒󠅢󠄟󠄮